Capabilities
Vertical Integration and Exceptional Techniques
Waterson Corporation has specialized in manufacturing metal products for over 40 years. Offering comprehensive capabilities as a one-stop shop, we transform raw material inputs into final products, bringing customers’ ideas to completion. Mastery of supply chain management allows seamless integration of cross-industry services from regional sub-suppliers, efficiently meeting customer demands. By working closely with clients, our engineering team ensures projects are completed with cost-effective methods, delivering products with ultimate feasibility and functionality.
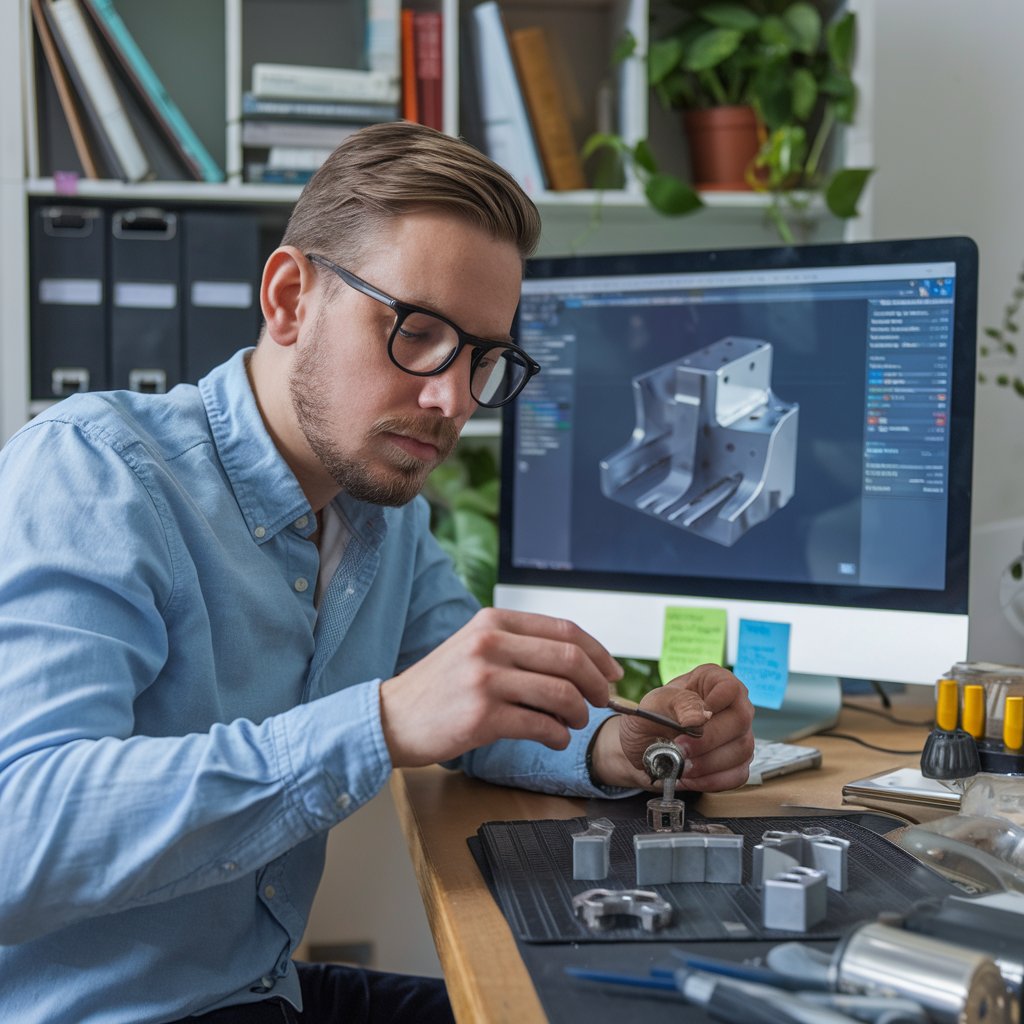
Design Engineering Expertise
Incorporates advanced design and engineering solutions
- Mold Flow Analysis
- Rapid Prototyping
- In-house Tooling
Precision Machining Excellence
Achieve precision as fine as ± 0.01mm
- Lathe Machining
- Vertical Milling Machining
- Horizontal Milling Machining
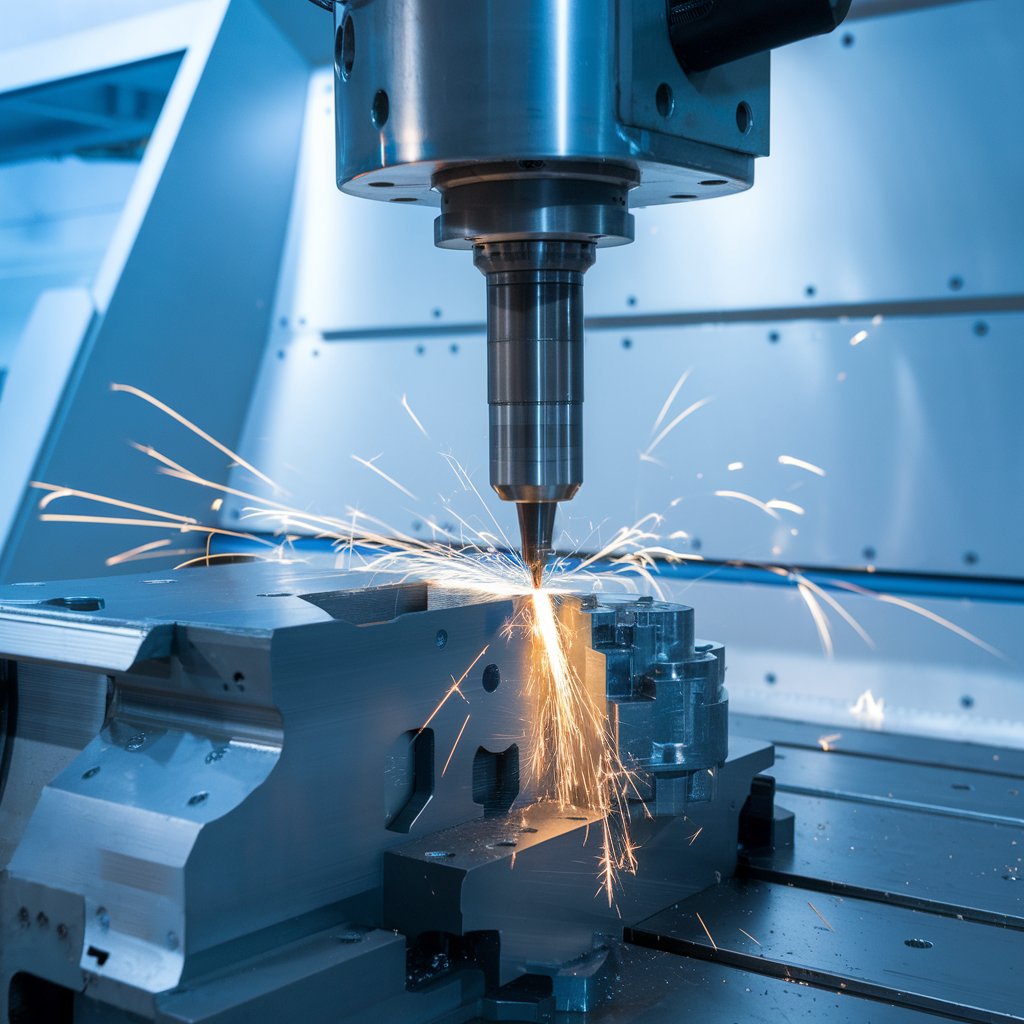
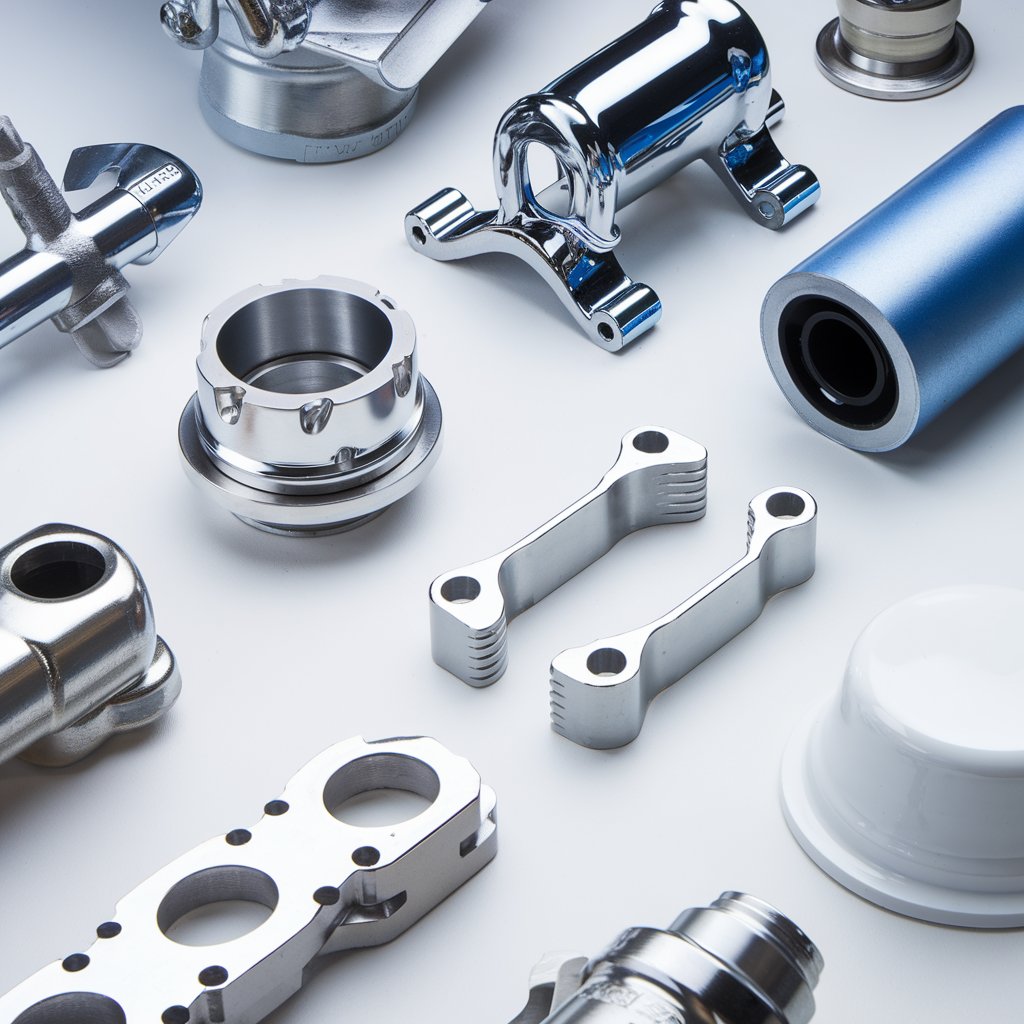
Diverse Surface Treatment
Features diverse surface treatments to achieve multiple application
- Polishing
- Electropolishing
- E-coating
- Powder Coating
- Liquid Coating
- PVD Coating
- Black Oxide
- Electroplating
- Chrome Plating
- Zinc Plating
High Quality Assurance
Features ISO-compliance, precise tolerances, smooth finish, and varied sizes
- Tolerance: compliance with ISO 2768-mK
- As-cast Roughness: typically maintaining 125 microinches (3.2 μm Ra)surface roughness, ranging from 60 to200 microinches
- Range of Size: up to a 10″ cube (250 mm³)
- Range of Weight: up to 50 pounds (25kg)
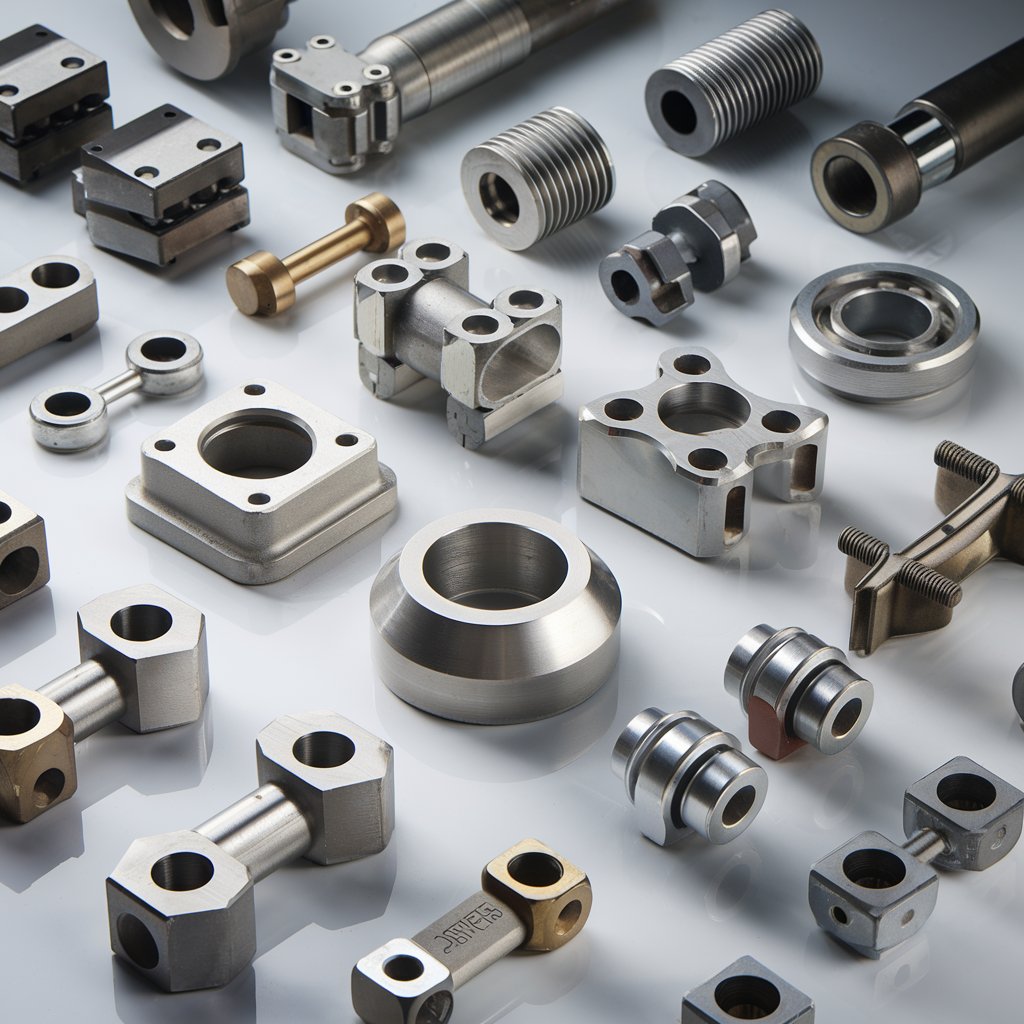
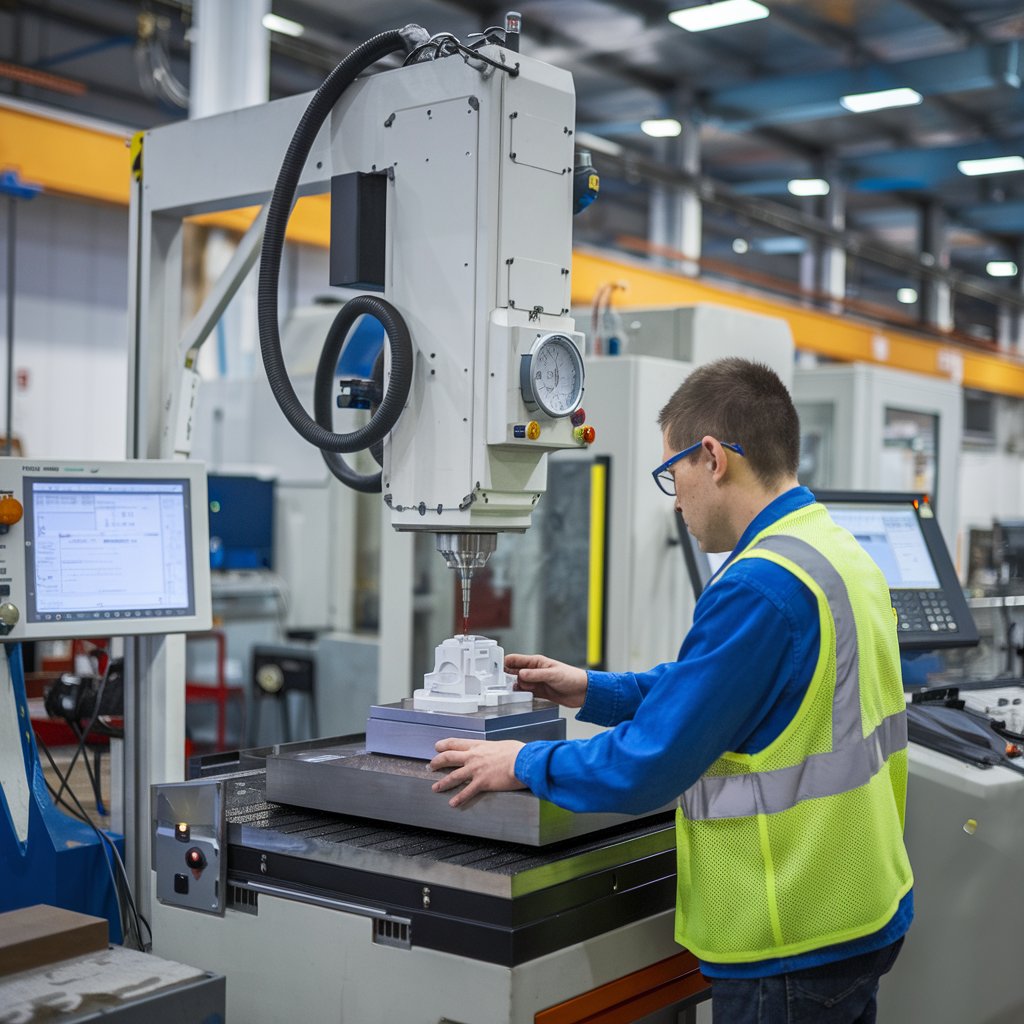
Precision Measuring Equipment
Equipped with precision measurement tools
- CMM(Coordinate Measuring Machine)
- Keyeance Optical Profilometers
- 3D-surface Profiler
- Mechanical Tesiting
- Equipment
- Colorimeter
- Glossmeter
- Height Guages
Precision Manufacturing Equipment
Employs advanced techniques in processing
- Heat Treatment
- Programmable Dip Coating Machine
- Robot-Assisted Machining
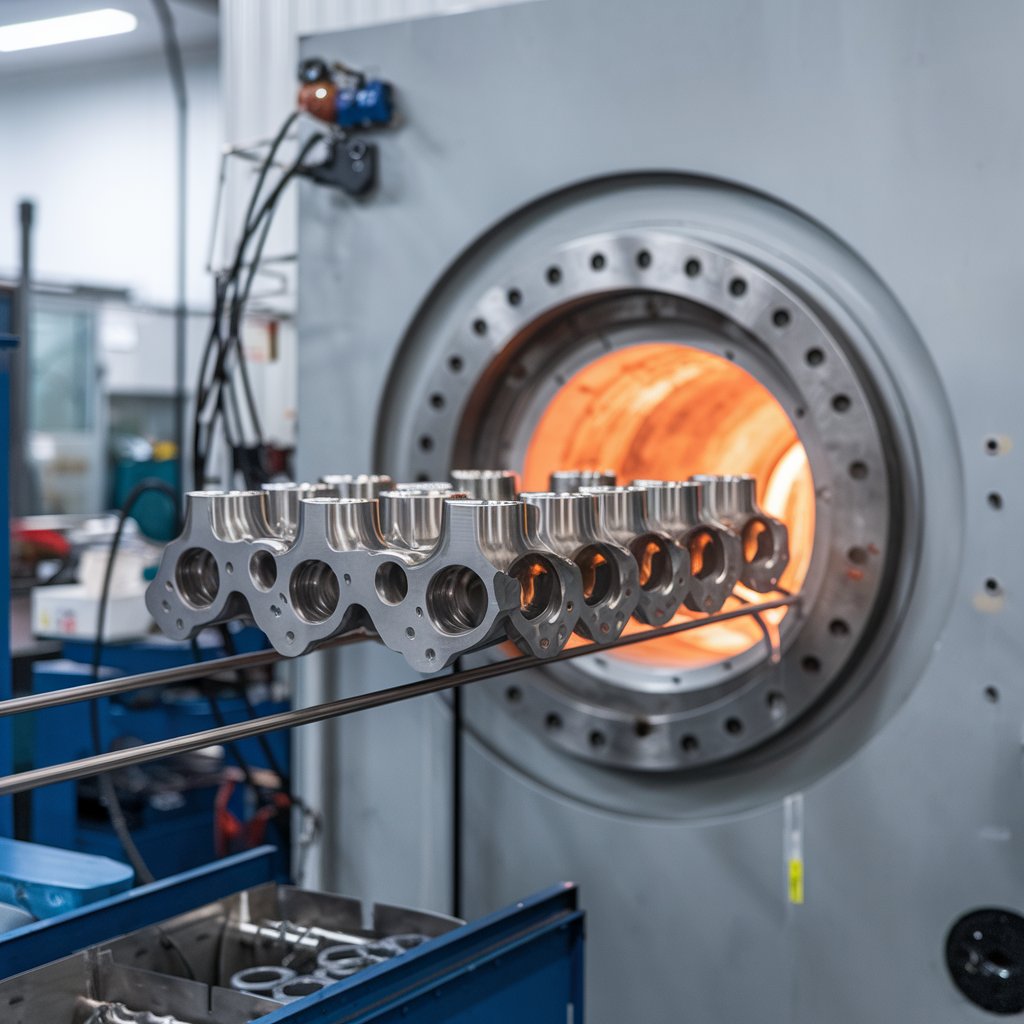
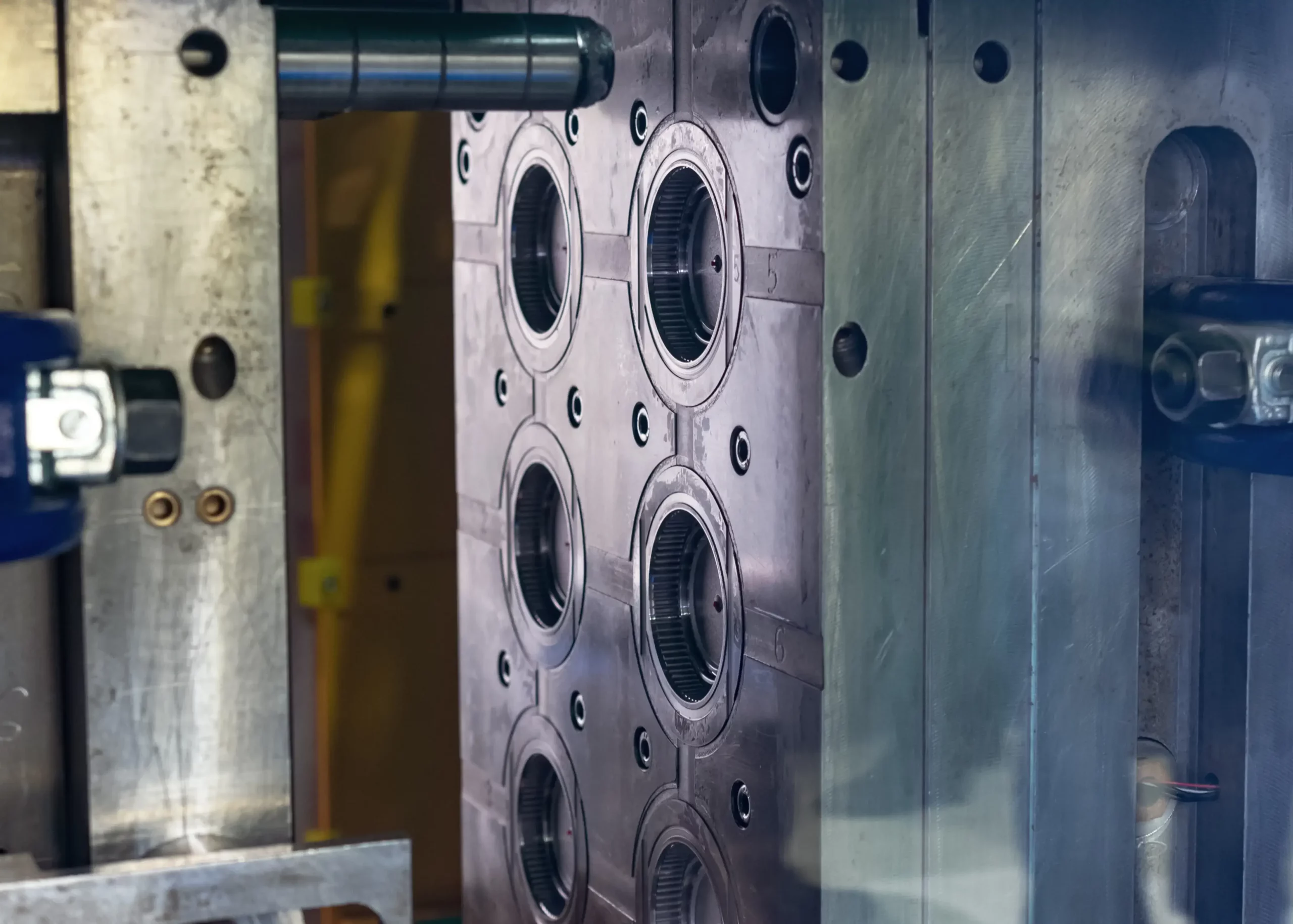
Design and Manufacture Molds
In-house tooling ensures exceptional accuracy and efficiency.
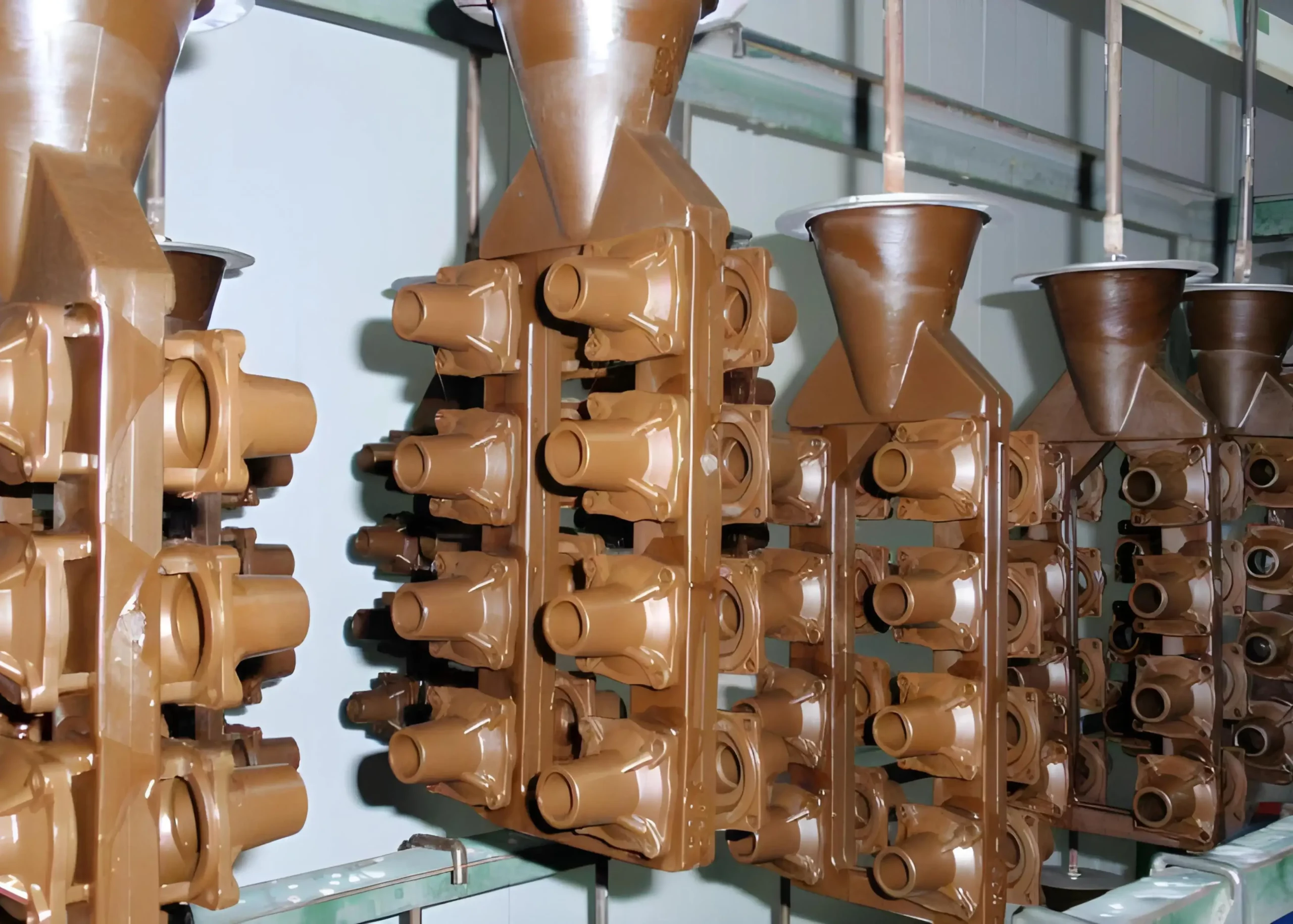
Wax Pattern Production
Advanced temperature control allows for dynamic adjustment and smooth flow.
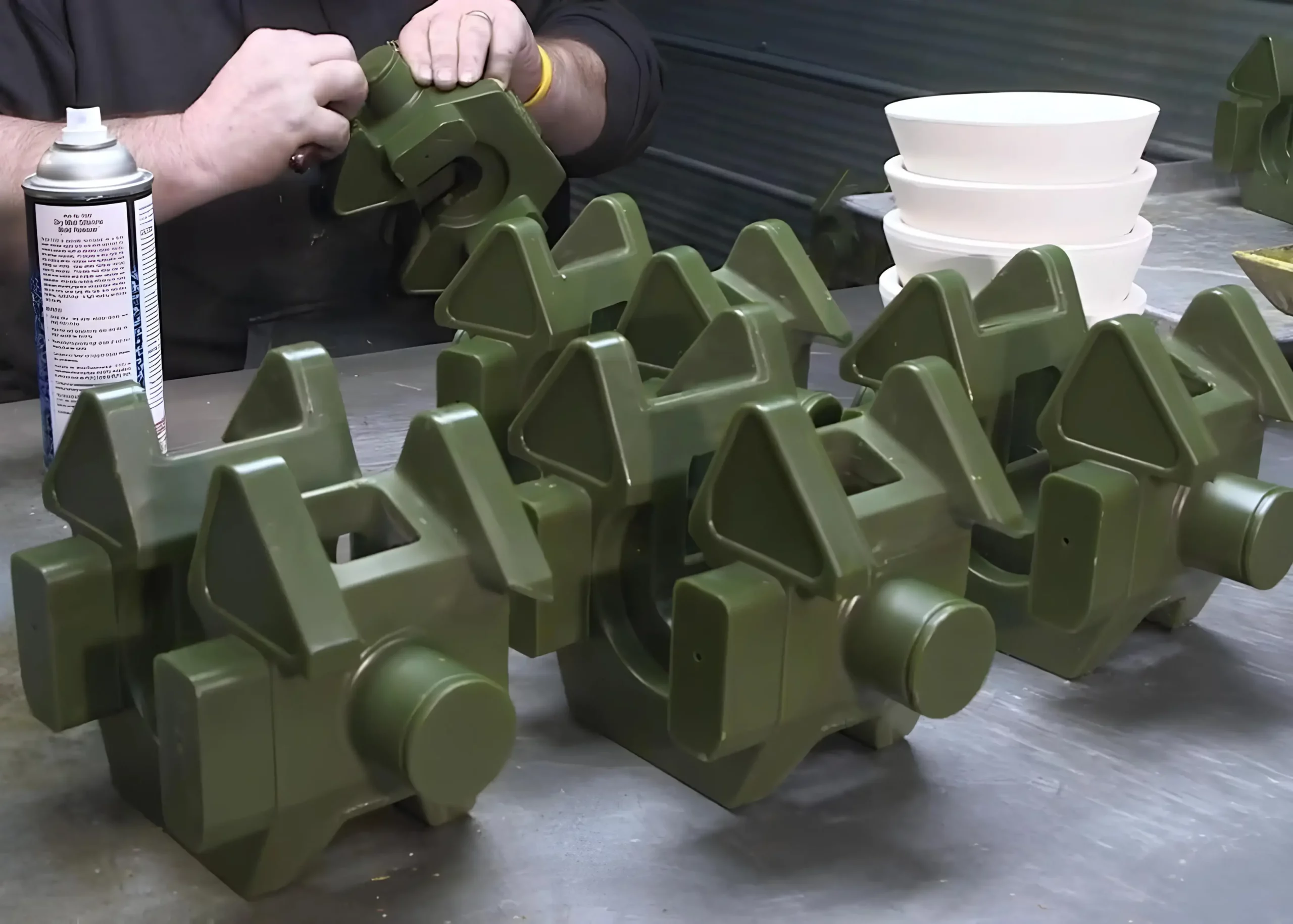
Wax Patterns Assembly
Skilled teams work with precise fixtures to create superior wax pattern trees.
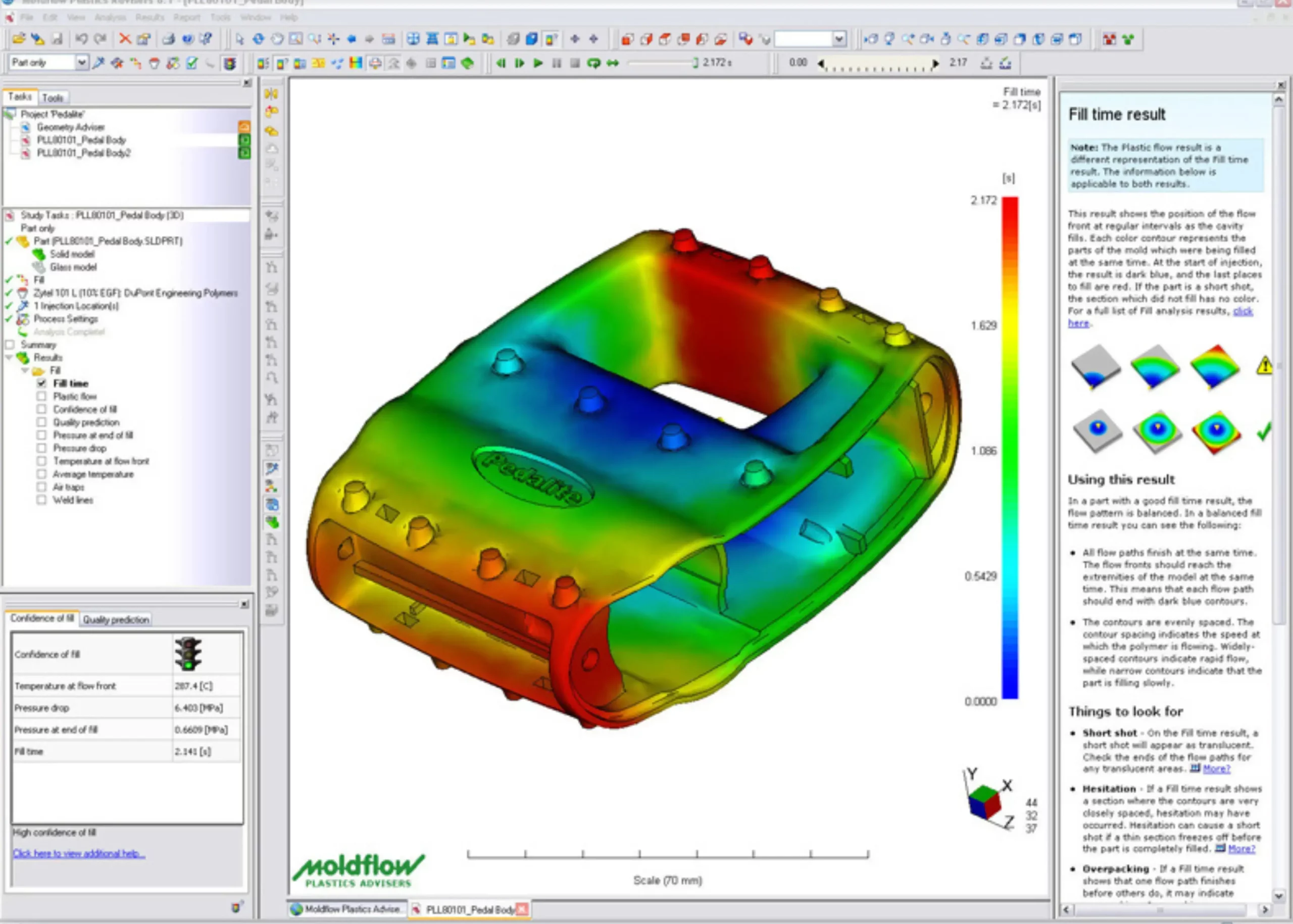
Mold Flow Analysis
Skilled engineers utilize advanced ProCAST software to analyze and formulate optimal tree designs.
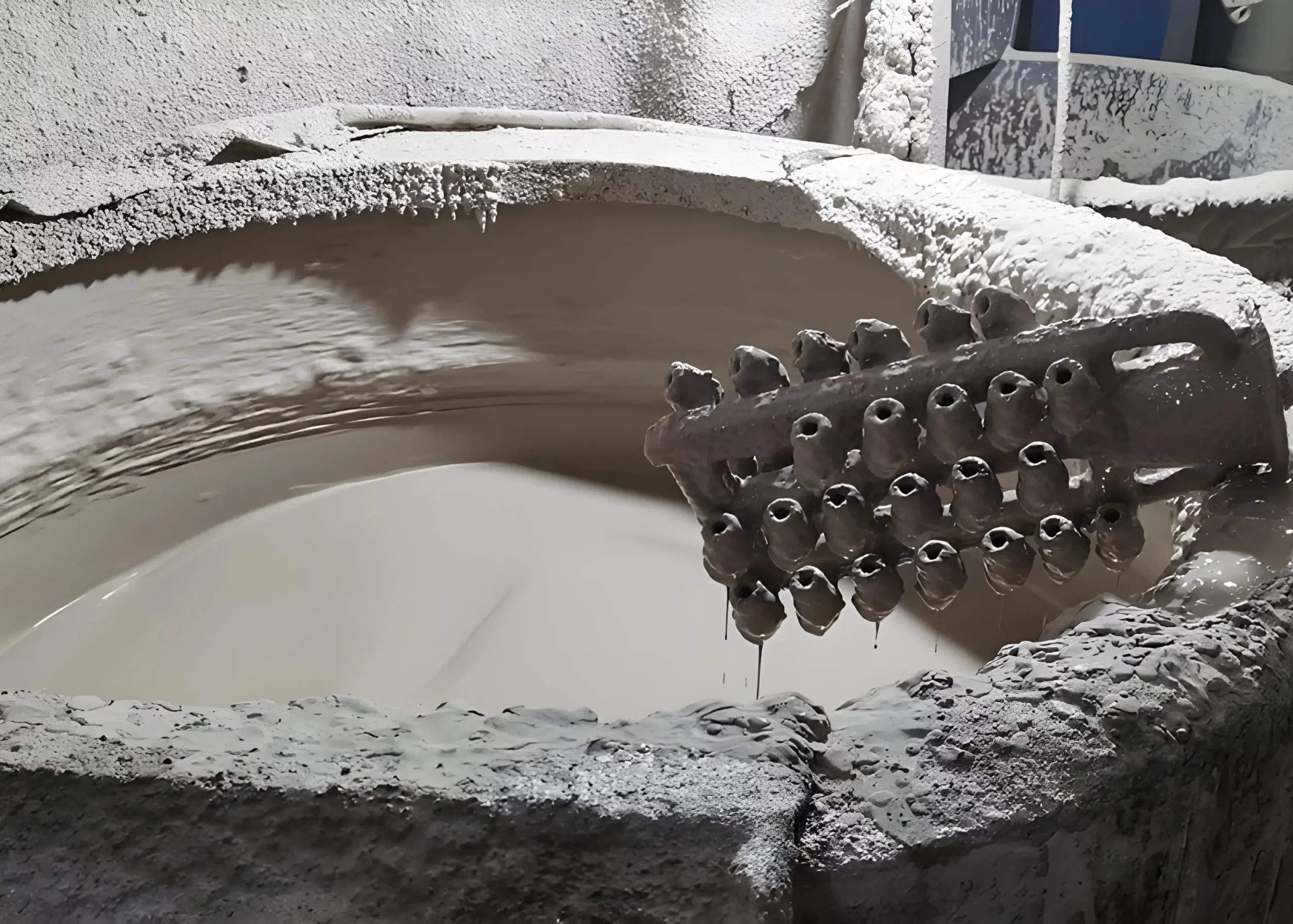
Shell Building
Dedicated and digitally-monitored drying rooms reduce dry time and overall expense.
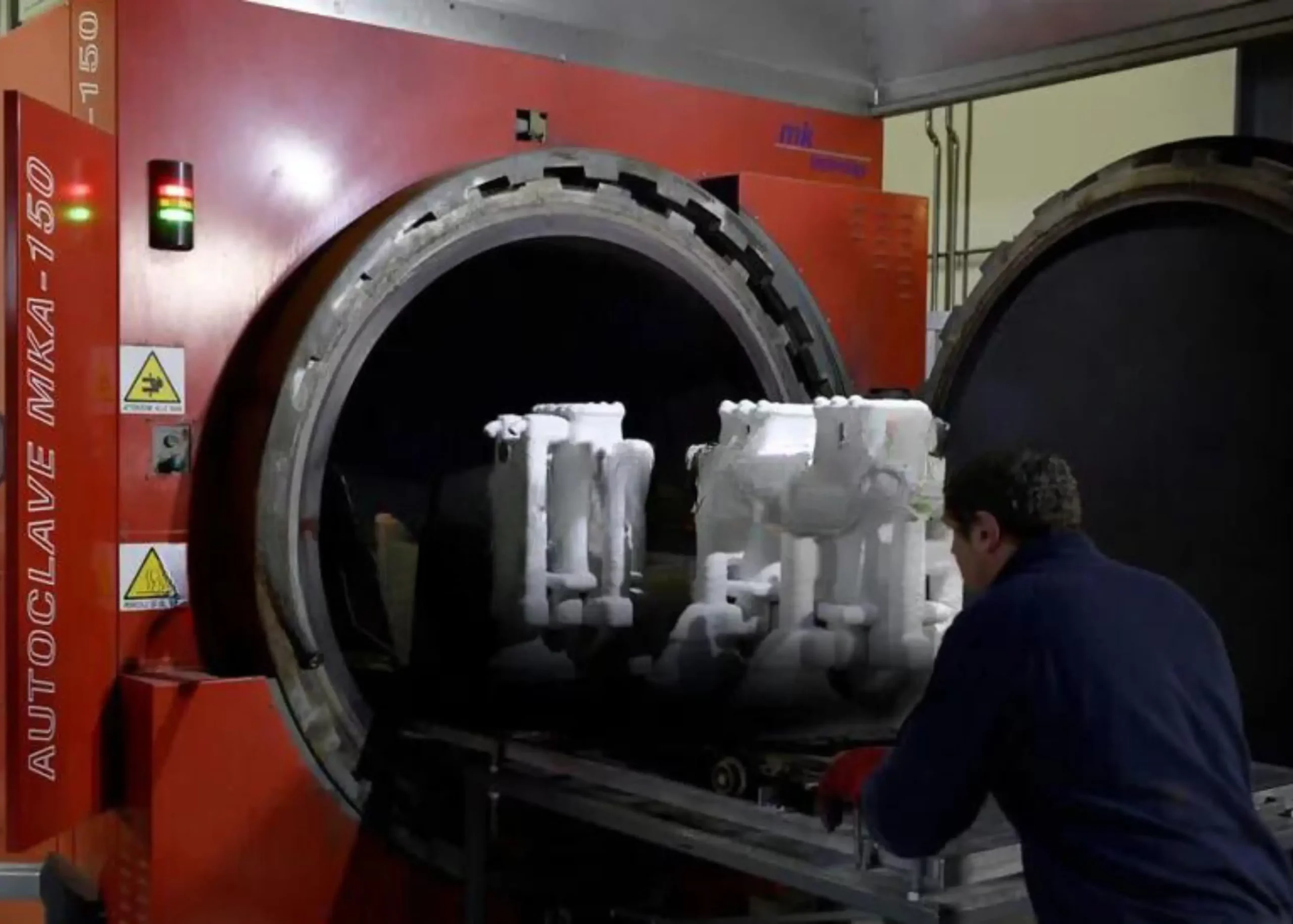
Dewaxing
Modern dewaxing machines save energy and reduces environmental impact, while improving employee safety.
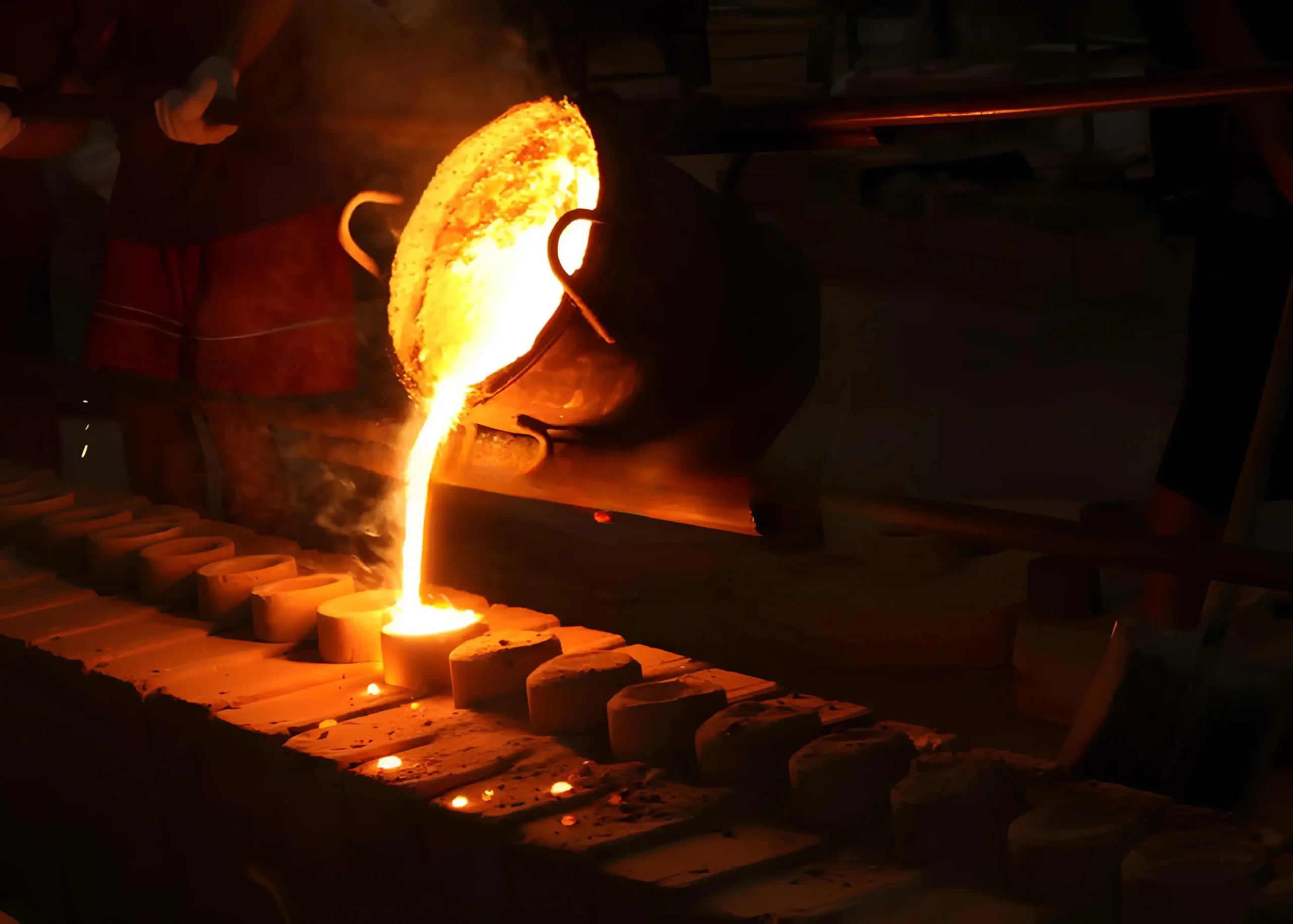
Molten Metal Pouring
Each batch is 100% spectrometer analyzed to ensure accurate composition and quality.
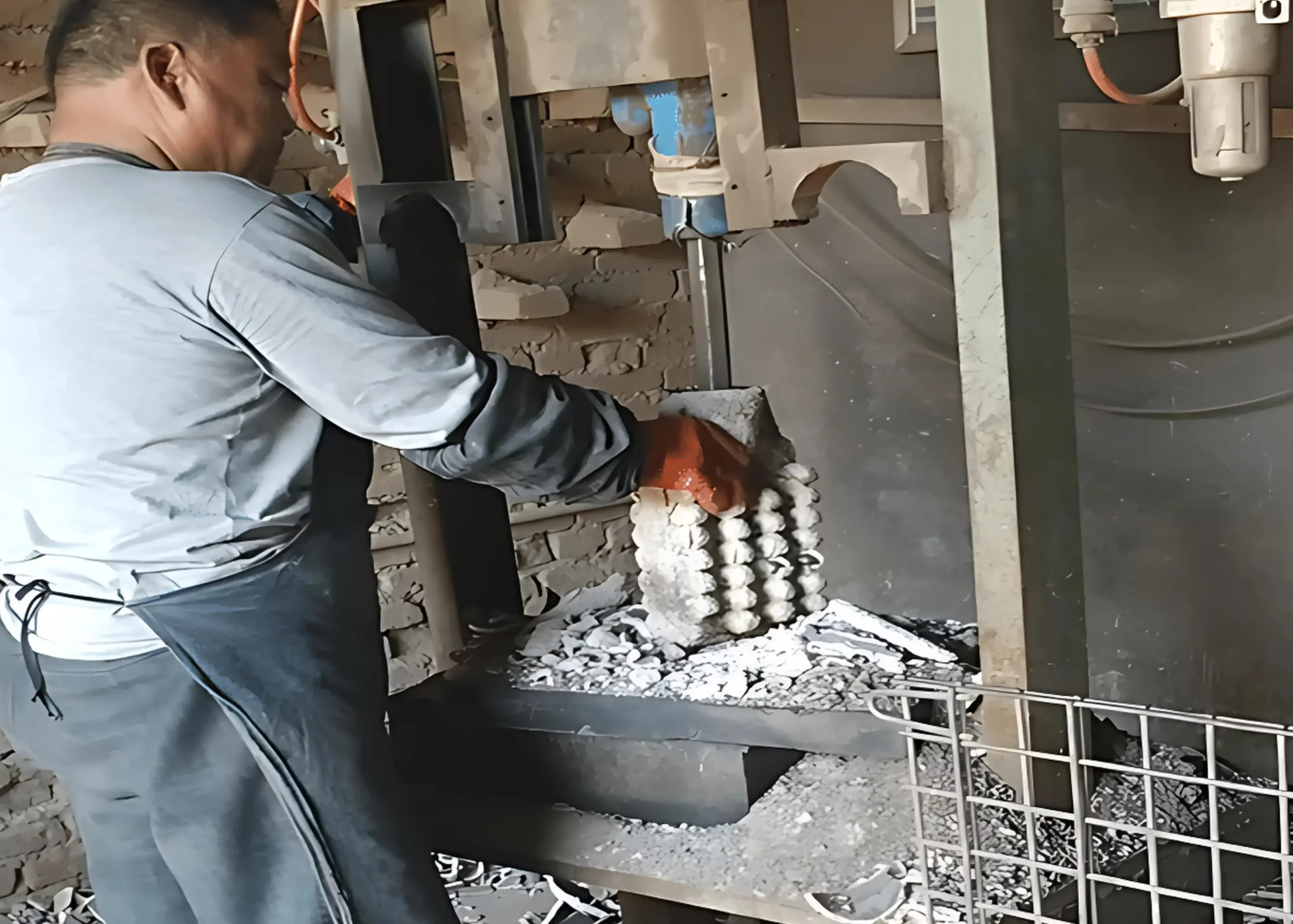
Shell Removal
Reduced process noise enhances employee productivity and overall quality.
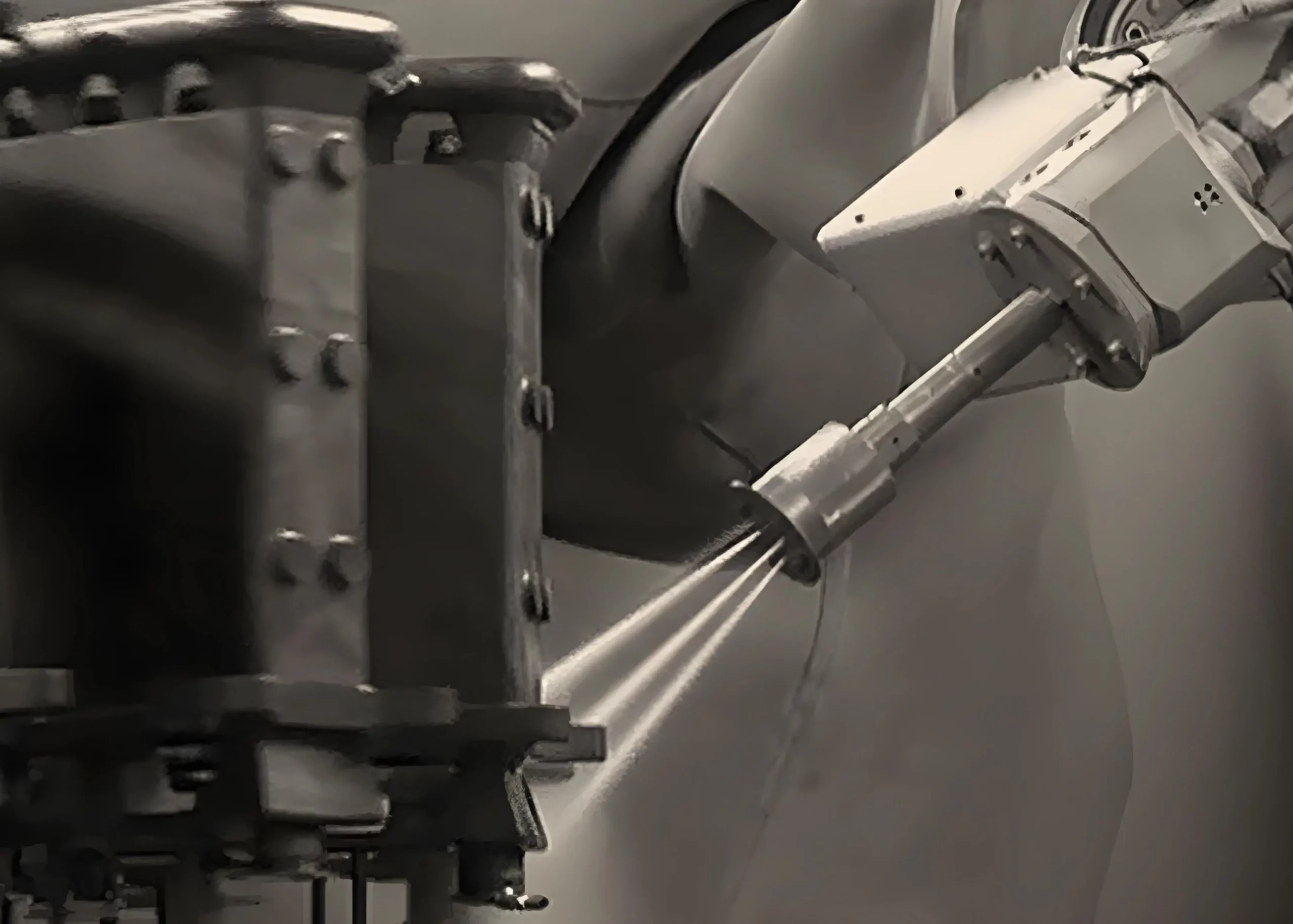
Casting Cleaning
Modern casting, pickling and alkaline cleaning machine ensures that parts are effectively passivated and comply with environmental standards.
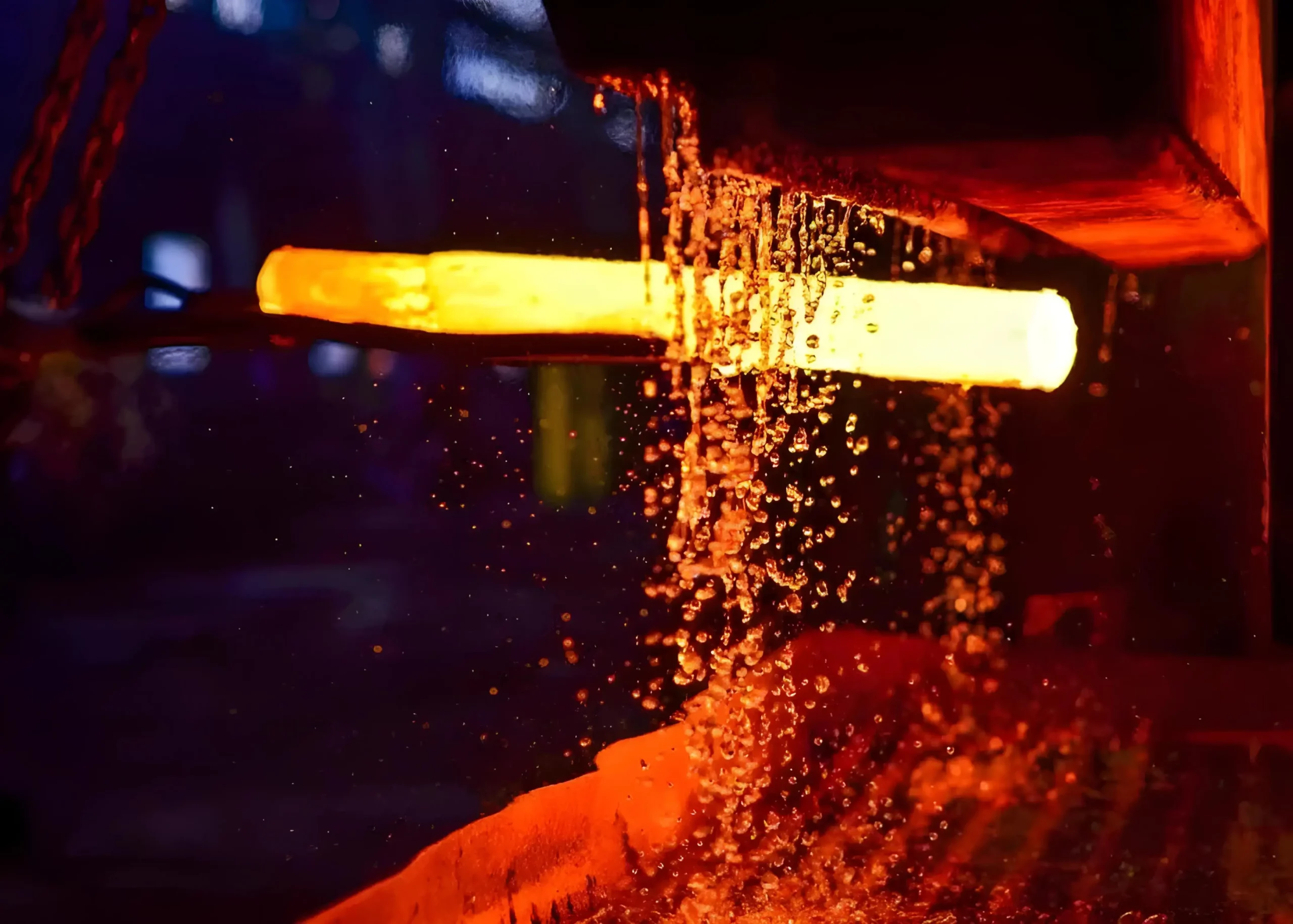
Heat Treatment
In-house heat treatment facility is operated by skilled engineers and technicians to insure that parts are properly annealed for machining.
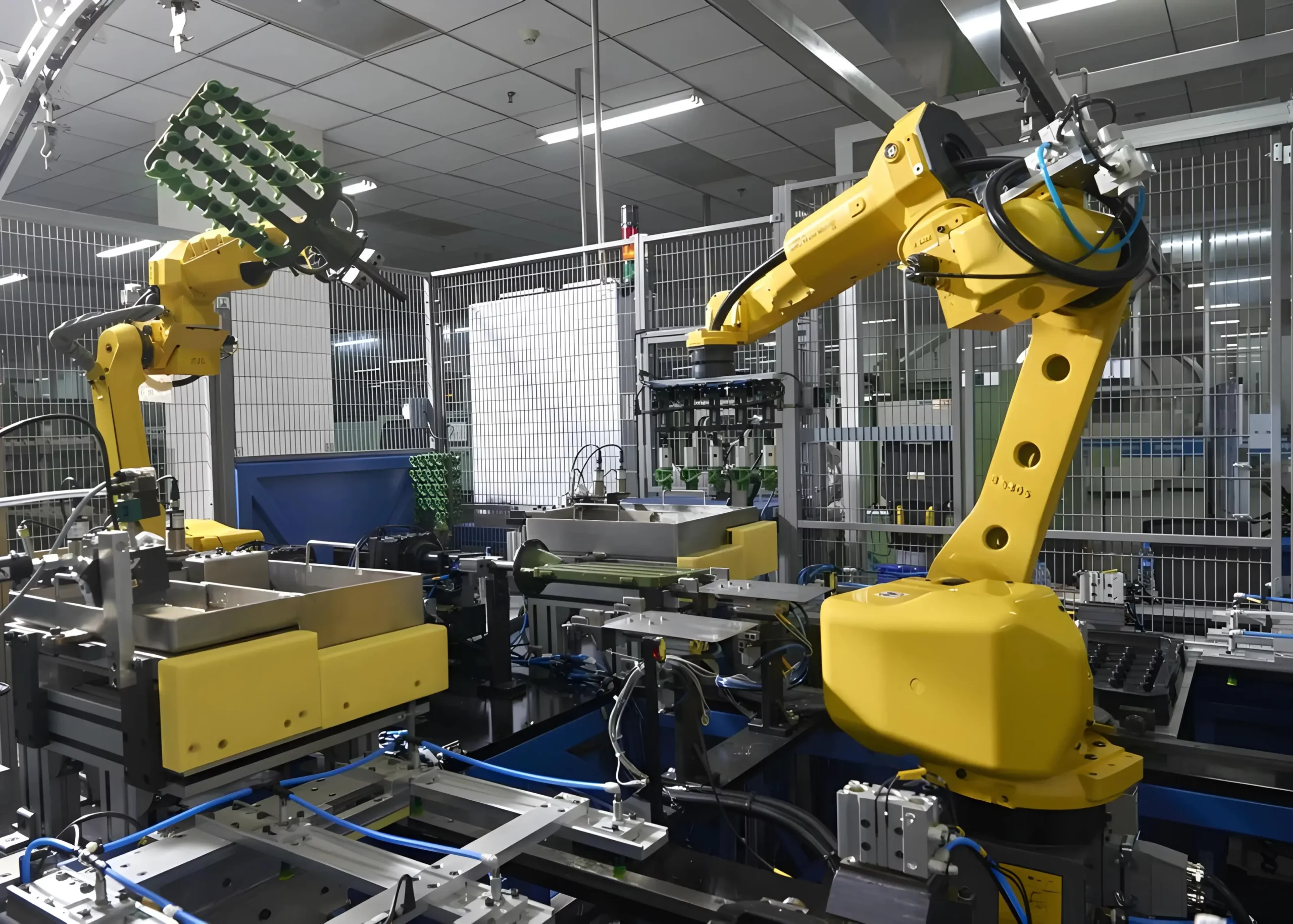
Machining
Decades of experience in all aspects of stainless steel machining, including drilling, threading, CNC, and more.
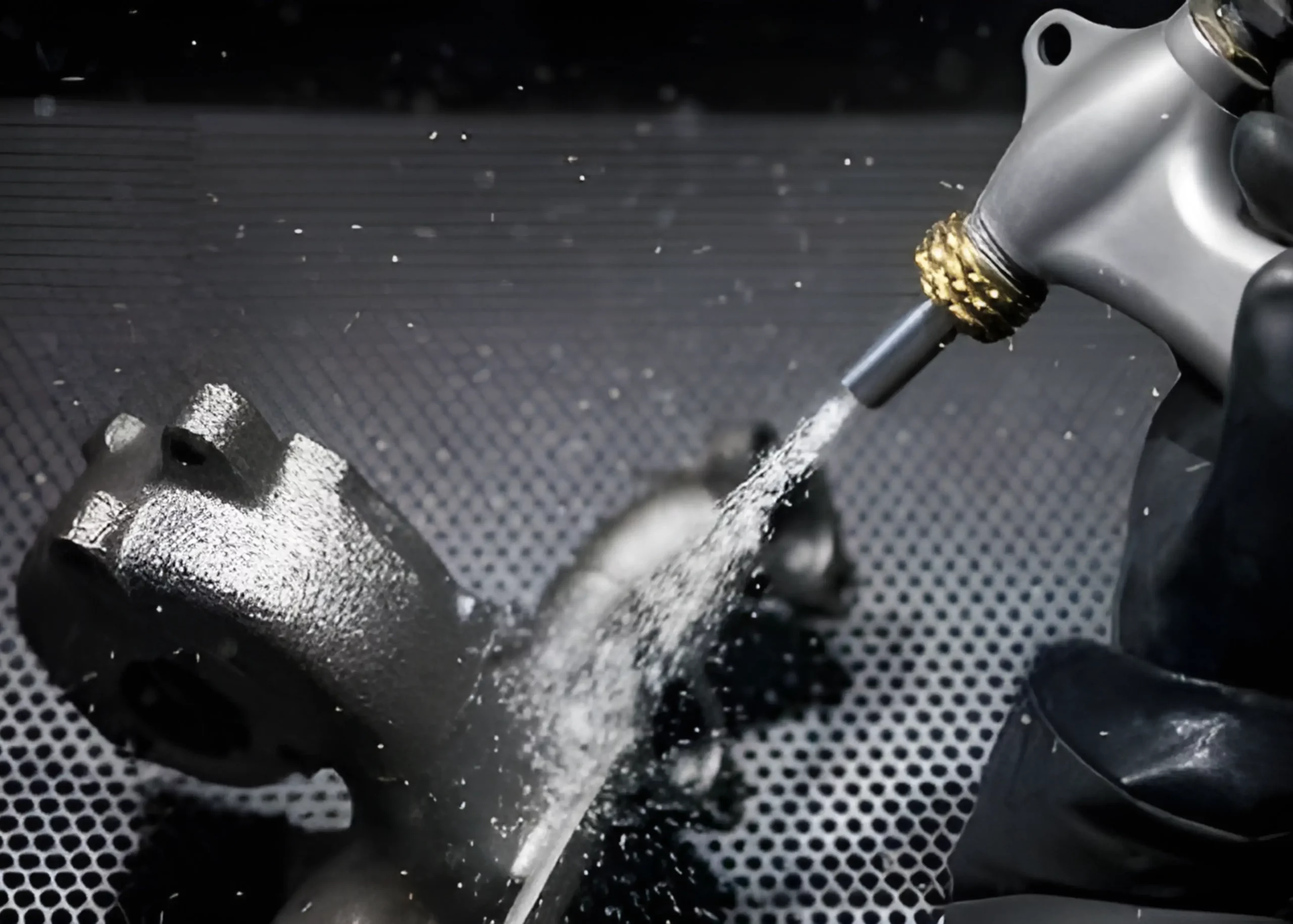
Surface Treatment
Skilled technicians and automated polishers are utilized to meet custom requirements.