Investment Casting
Elite Investment Casting Process Overview
Waterson specializes in stainless steel investment casting, delivering high-quality components with a focus on precision and durability. We operate fully-integrated design and manufacturing facilities, which produce products for a variety of industries including door hardware, petrochemical and medical, to name a few.
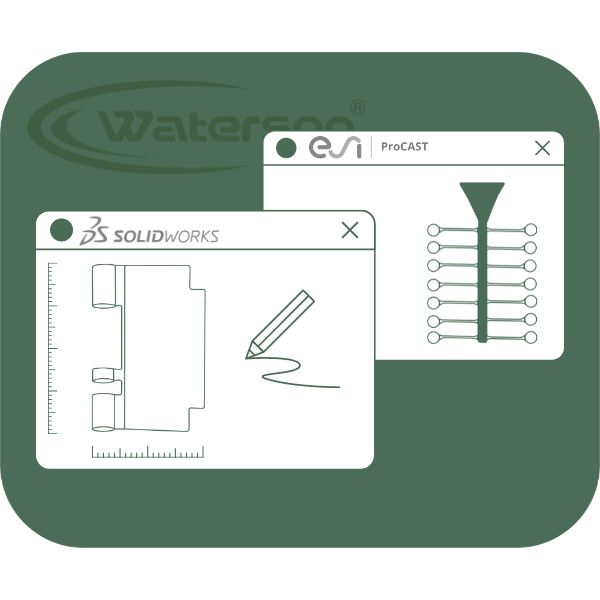
Step 1: Design & Engineering
Waterson Coporation utilizes Solidworks software to formulate your creative design. Also, by employing ProCAST software to conduct cast analysis, this eliminates the concerns and errors in the early engineering development, avoiding casting failure, and fine tuning the engineering design model to ensure high-quality in the cost- effective manner.
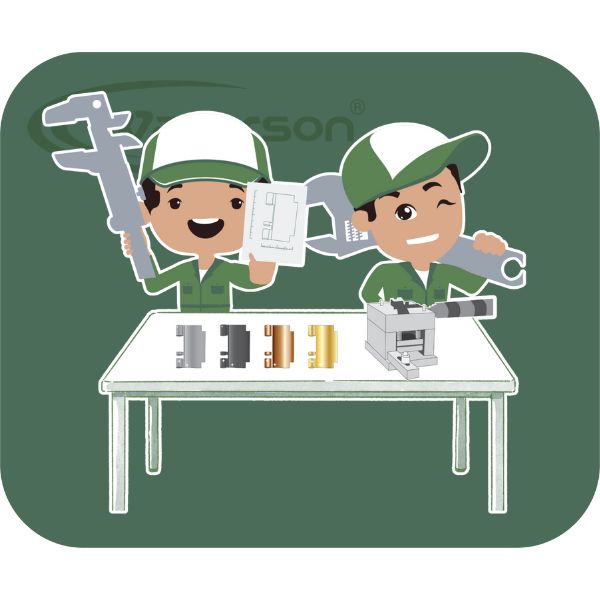
Step 2: In-House Tooling
With skilled technicians and engineers, Waterson can immediately respond to the dimensional and quality issues to comply with engineer’s design. This allows us to quickly diagnose any concerns in creating tooling before manufacturing the casting.

Step 3: Wax Injection
With real-time monitoring and controllable parameters during wax injection process, Waterson can generate higher production yields and stabilize dimensions. By utilizing cooling fixtures, our team can effectively ensure wax pattern to be consistent before cooling down to room temperature.
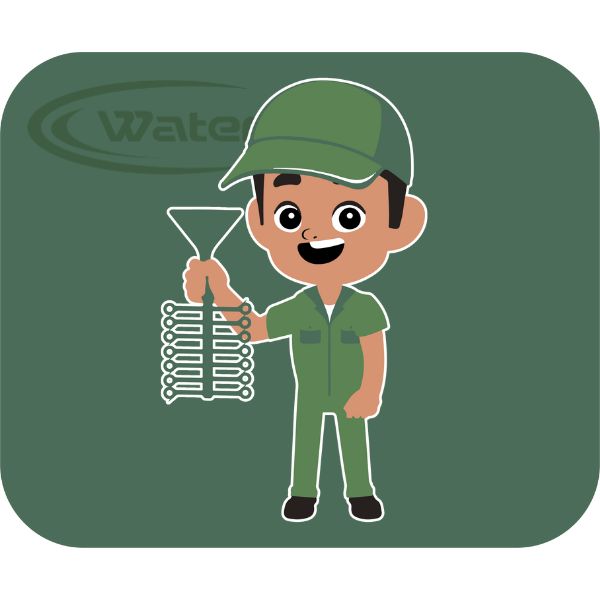
Step 4: Wax Tree Assembly
Building wax tree assembly is a sophisticated process that requires skilled profession and abundant experiences since it influences on the outputs of the casting parts. Skilled technicians in Waterson Corporation are well-trained to manually assemble wax patterns onto runner. Once the wax tree assembly is finished, then it is ready to be dipped.
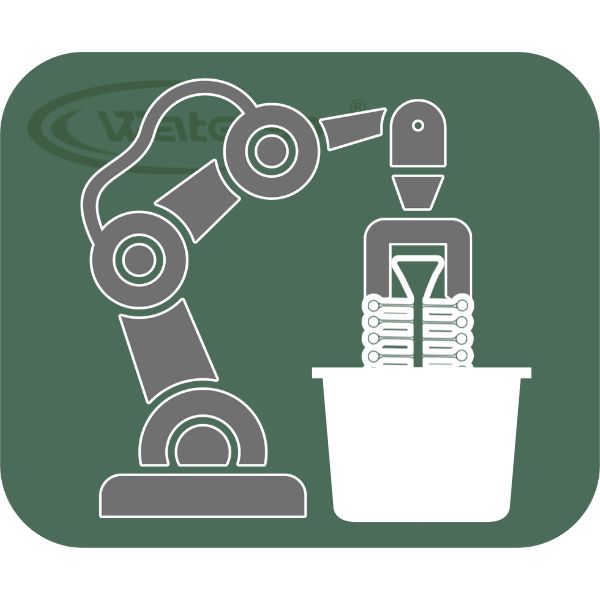
Step 5: Shell Coating
Waterson Corporation employs 6 axis robotic arm in dipping lines to create even surfaces across the trees to increase a greater level of consistency in productivity. This process of dipping requires 4-5 times repeatedly.
To ensure high quality of shells, we monitor temperature and humidity in shell environment.
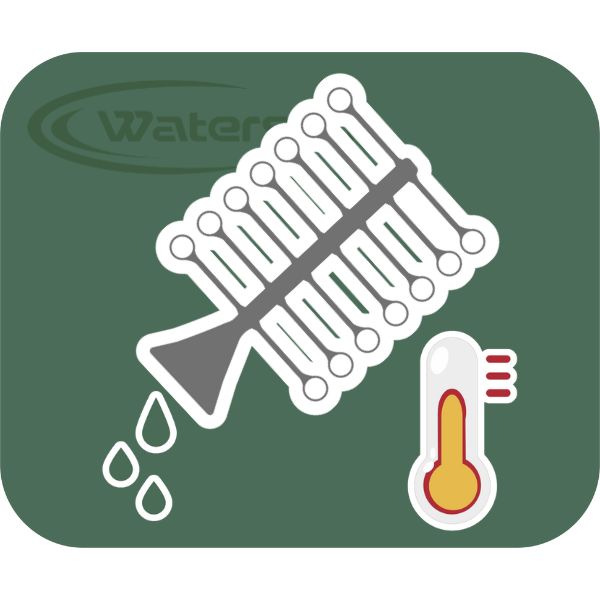
Step 6: Dewaxing
Removal of the wax from ceramic shells can be done by using steam in an autoclave. The used wax can be recyclable for future production to reduce environmental waste.
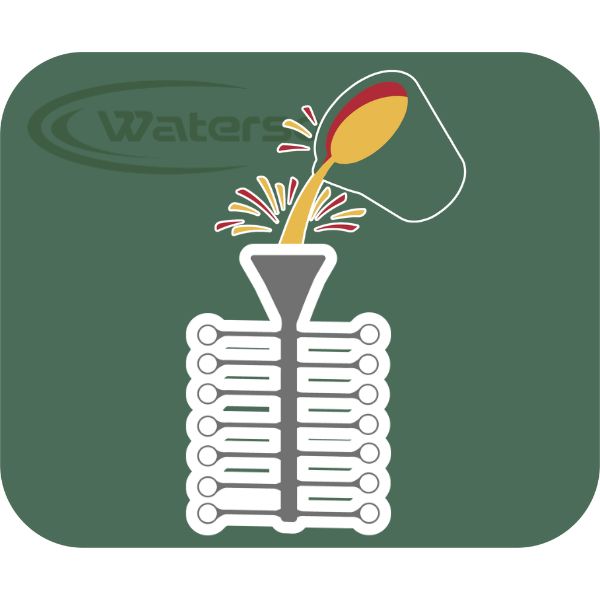
Step 7: Pouring
Waterson Corporation aims to provide extraordinary casting quality that meets the international standards. By using spectrometer, the chemical compositions can be analyzed systematically. Desired molten metal alloy is ready to pour into 1100℃ baked shells.
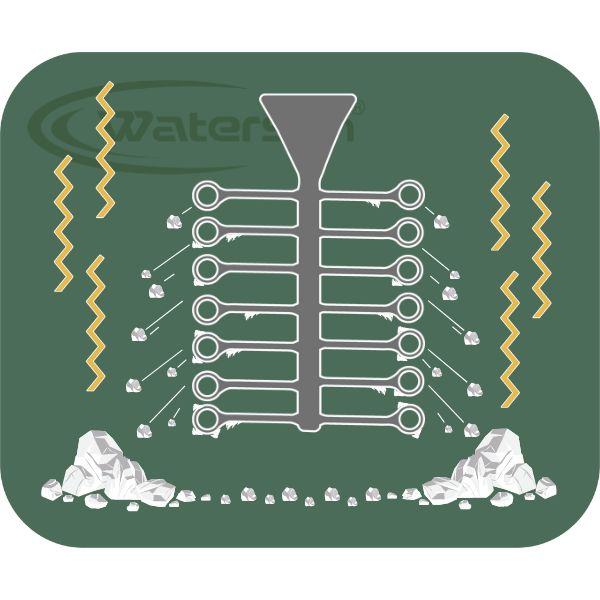
Step 8: Shell Removal
Once the ceramic shell is cooled down, shell materials can be physically knocked off by means of automatic vibration machine.
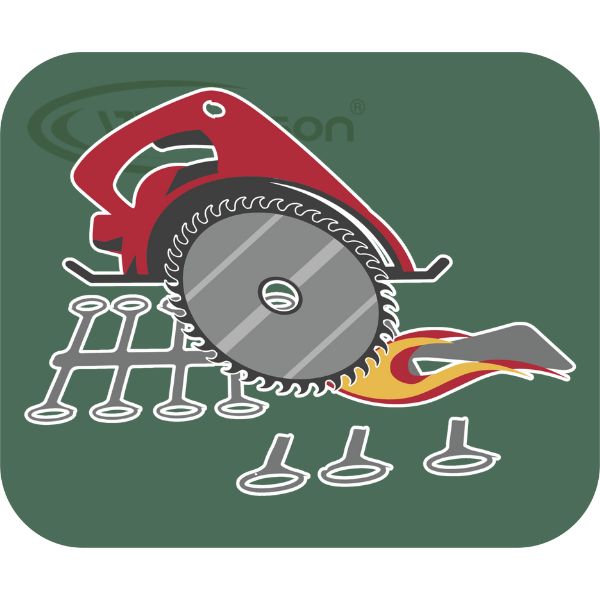
Step 9: Cut Off
Skilled technicians cut off the investment casting parts from sprue to separate the patterns from casting body. Considering labor safety and cost efficiency, semi-automation is needed.
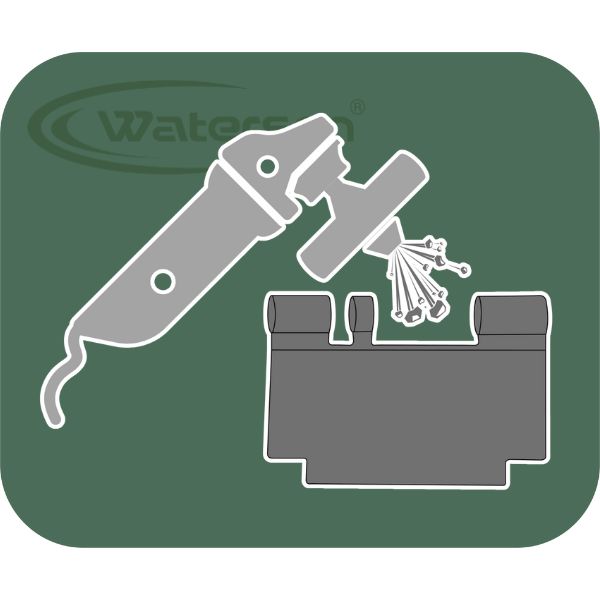
Step 10: Bead Blasting & Sand Blasting
To ensure excellent quality of casting, we also utilize bead blasting to make the casting surface a bright and consistent satin-like appearance.
To create a finer casting surface, glass bead blasting is used to shape brighter appearances.
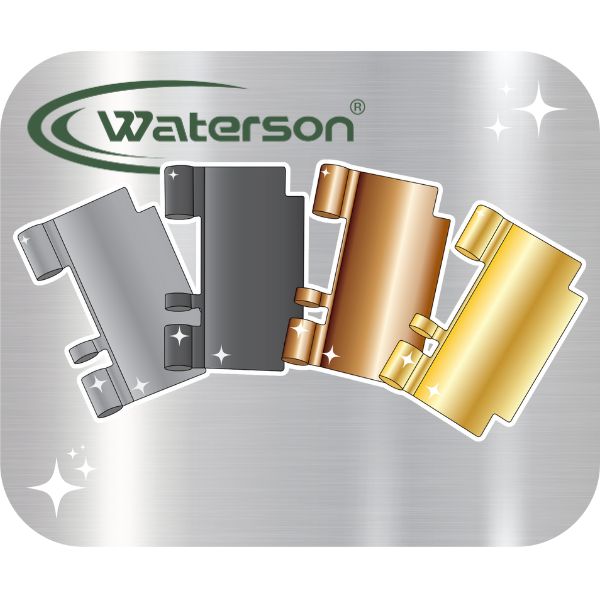
Step 11: Finishing
Multiple finishing approaches are utilized including grinding, blasting, welding, and plating. Waterson Corporation also offer diverse surface treatment, such as chrome plating, e-coating, powder coating, passivate, and vibratory finishing. We commit to providing metal products of superior surface quality for customers involving in multiple industries.
Corrosion Resistant Stainless Steel Alloys
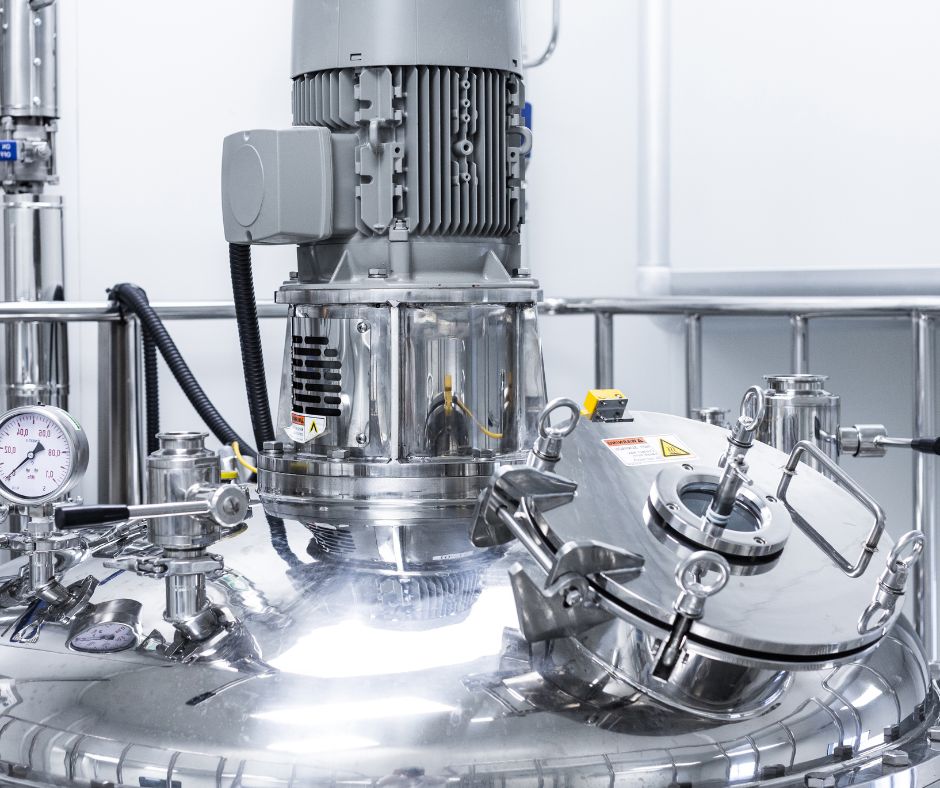
Commercial Use 304(CF8)
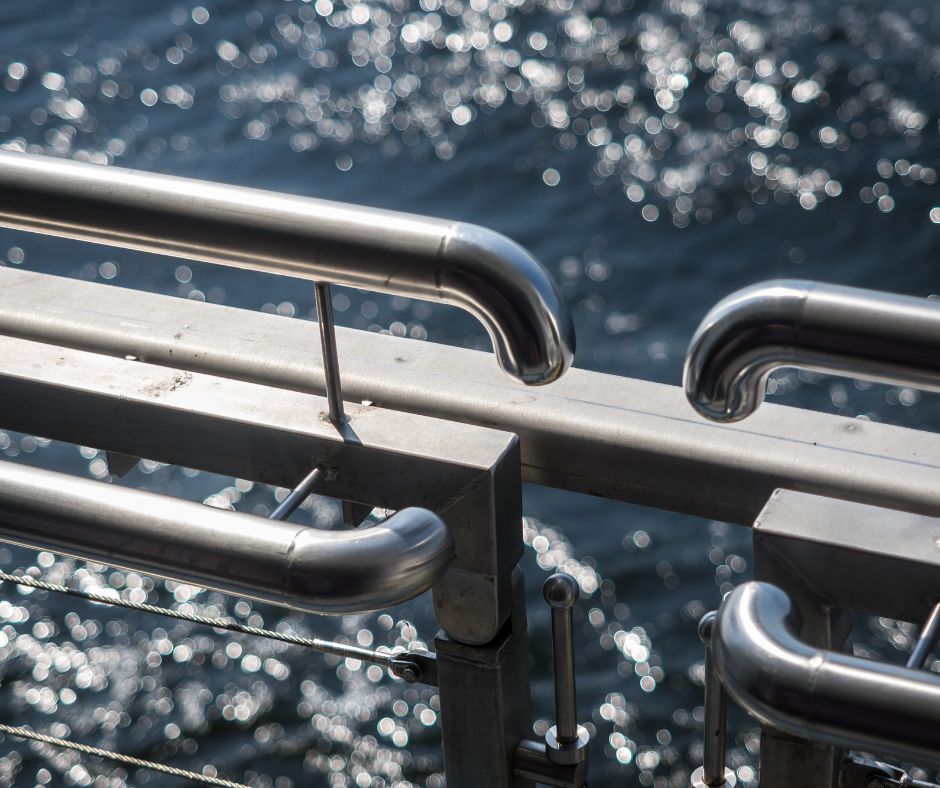
Marine Grade 316(CF8M)
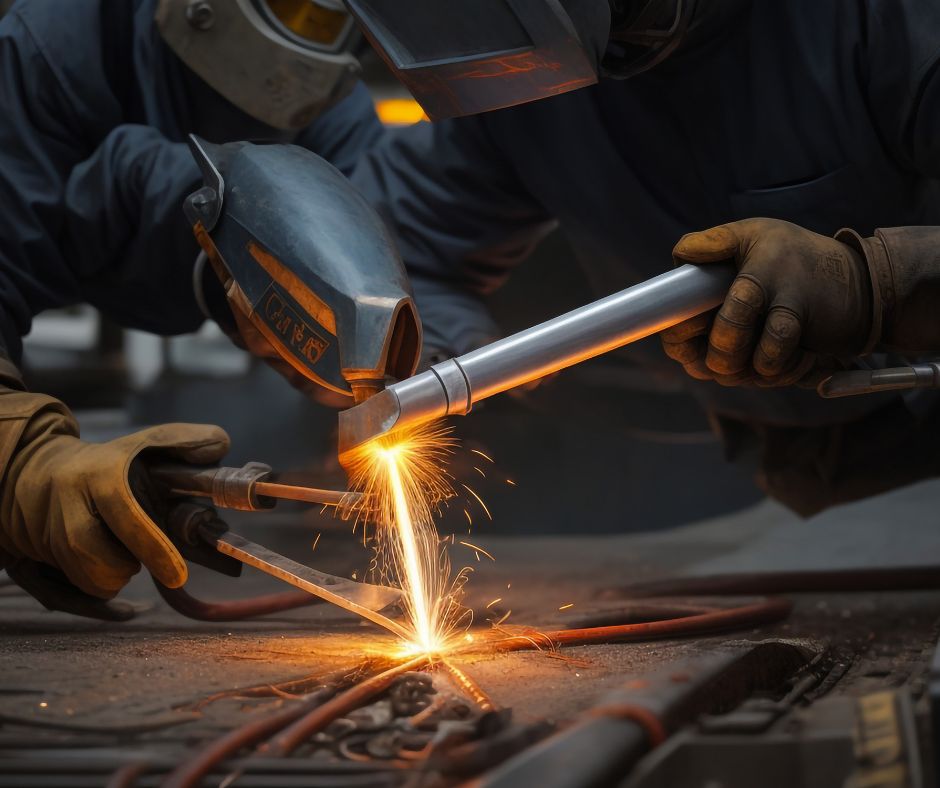
Exceptional Weldability (304L)
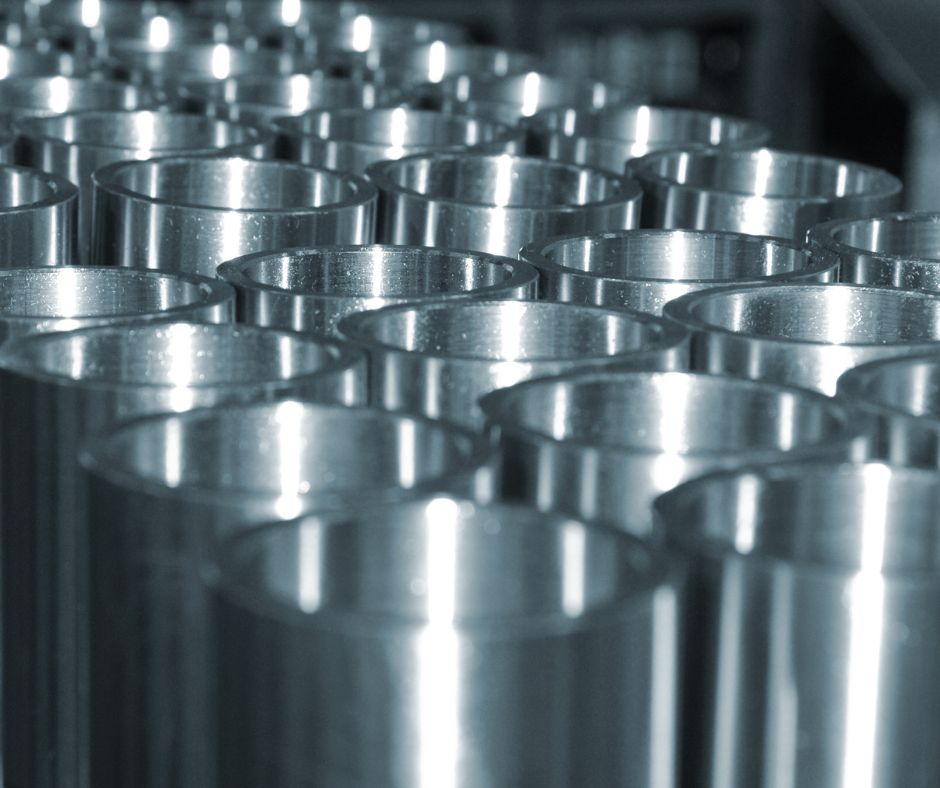
Enhanced Corrosion Resistant 316L
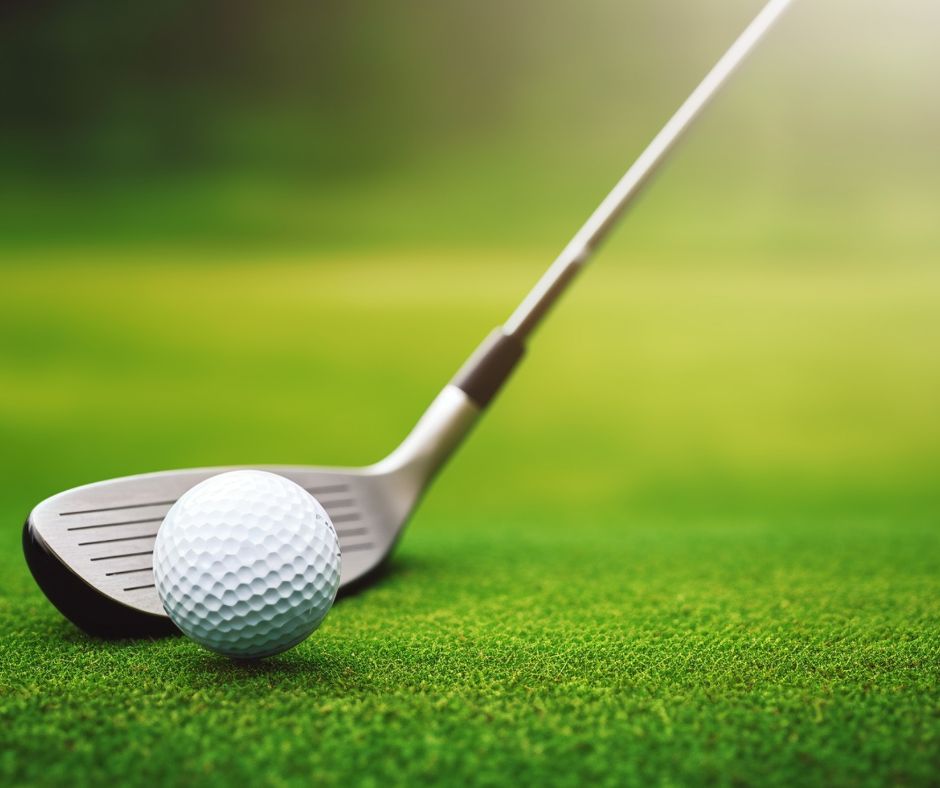
High Hardness 420
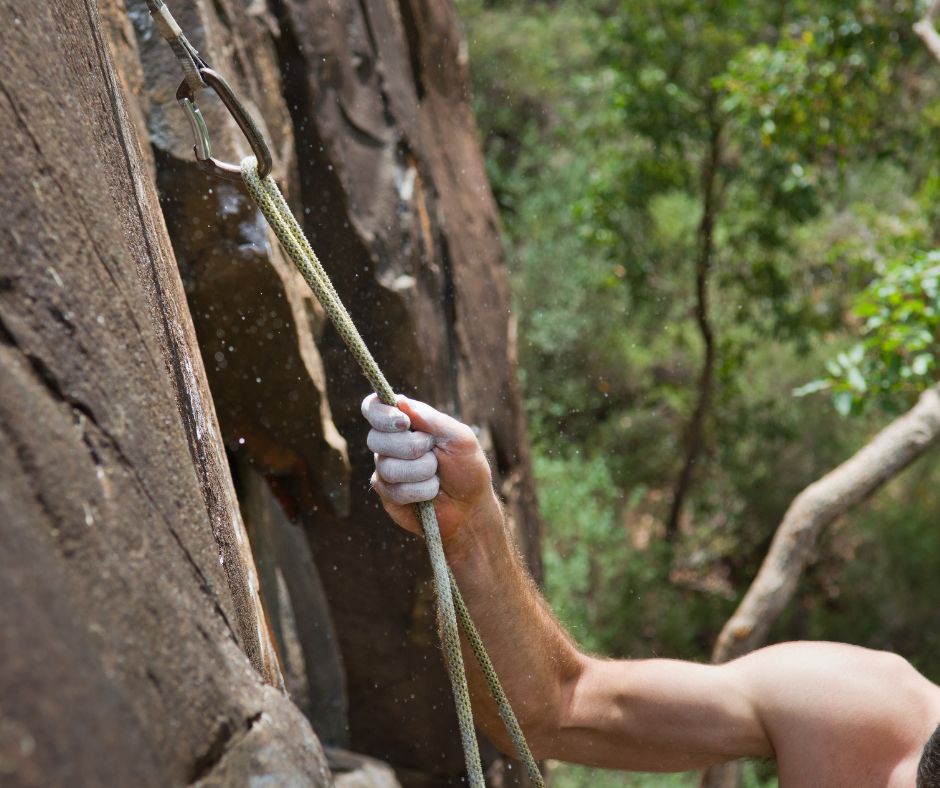
High Strength (17-4)
Across All Industries
Waterson precision investment casting manufacturer is capable of producing high quality components in many industries.
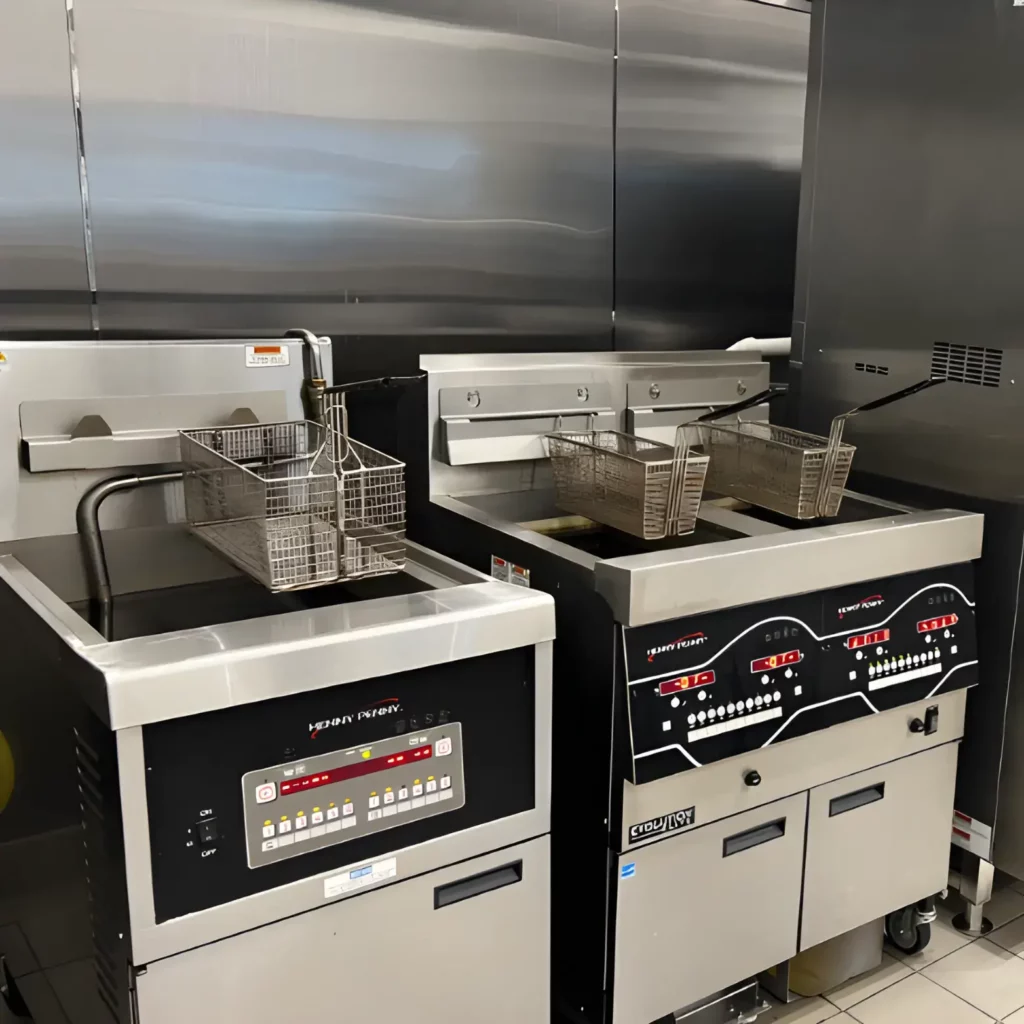
Restaurant Equipment
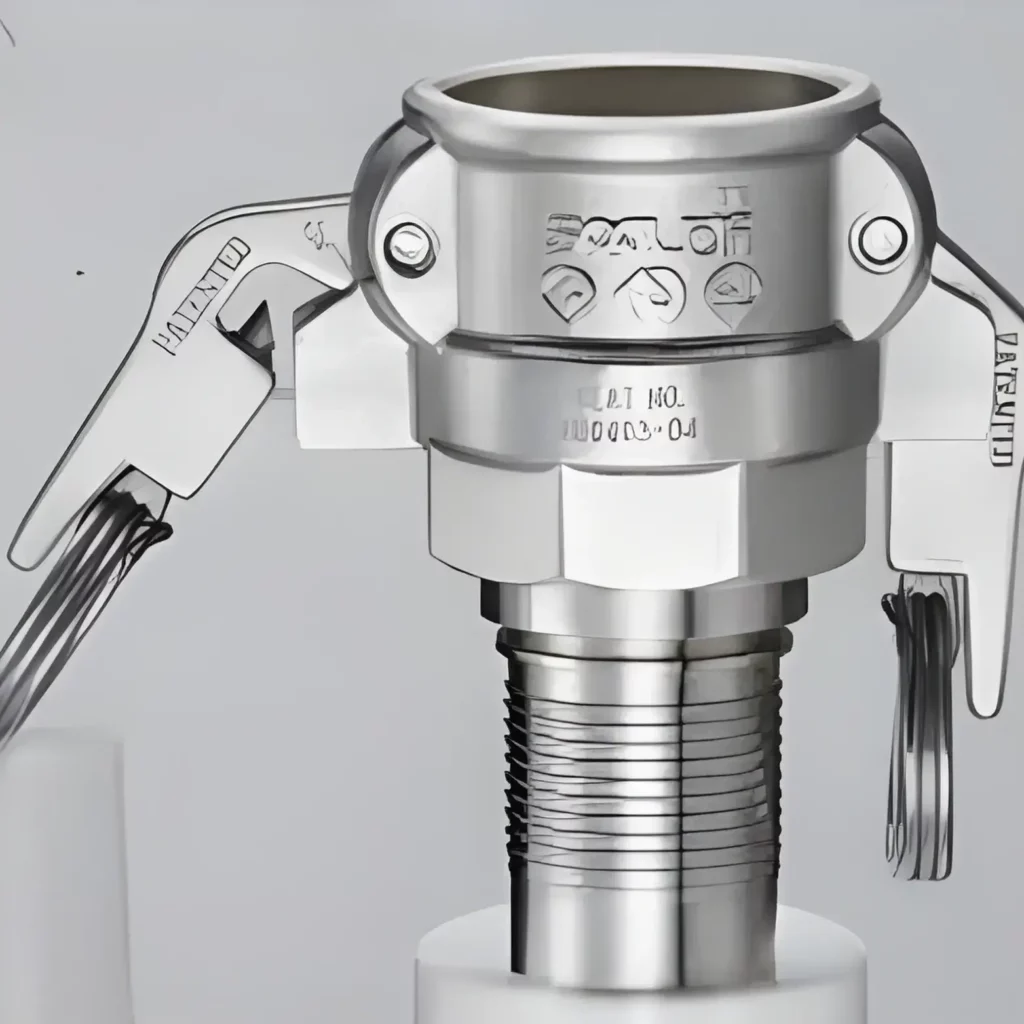
Petro Chemical
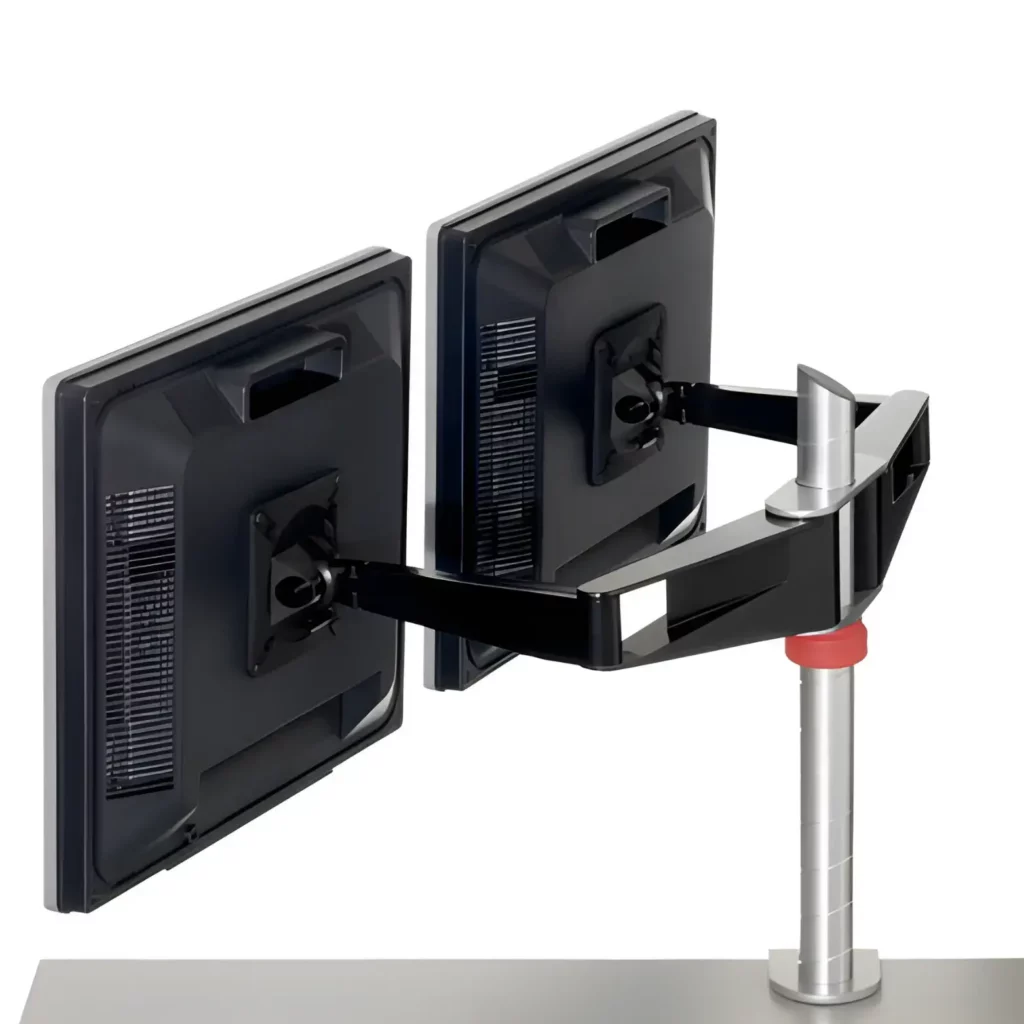
Furnitures
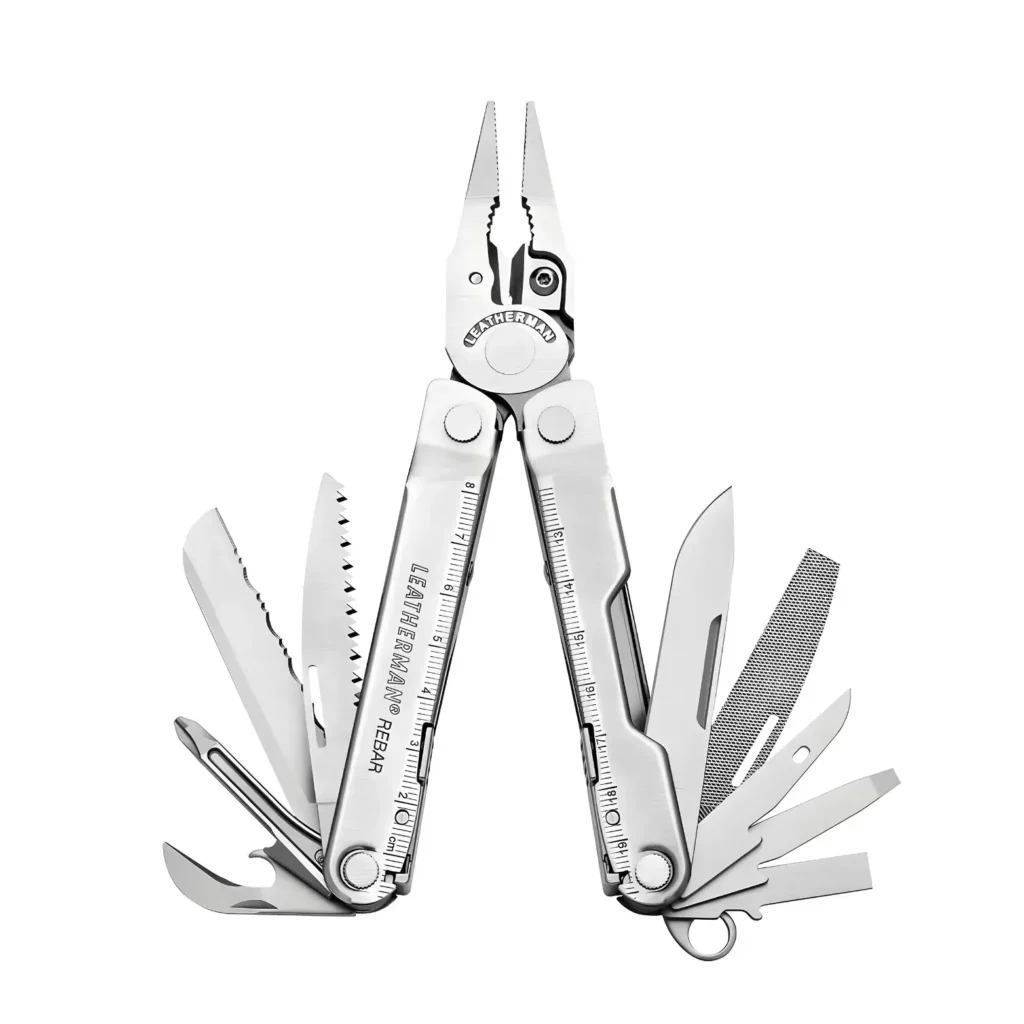
Tools

Hardware
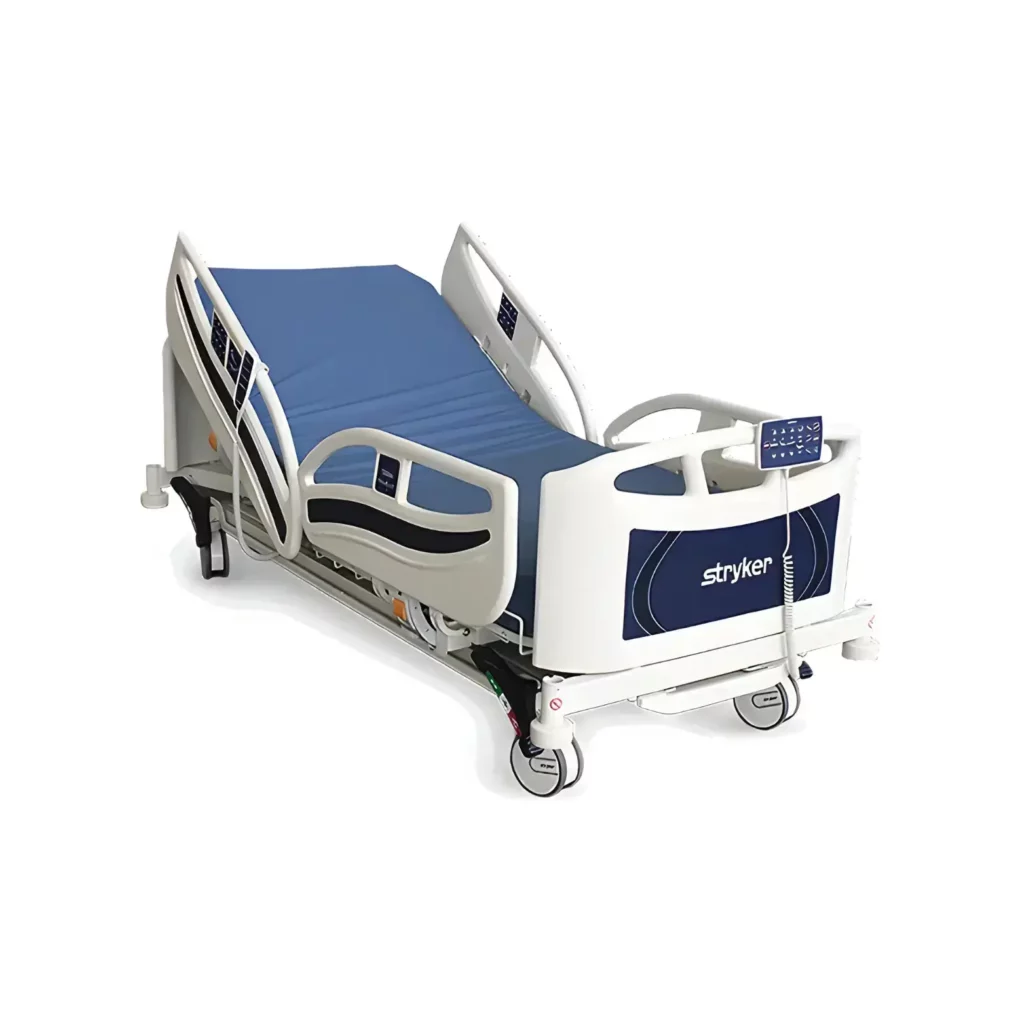